On Materials
Analysis and ideas on the future of advanced materials
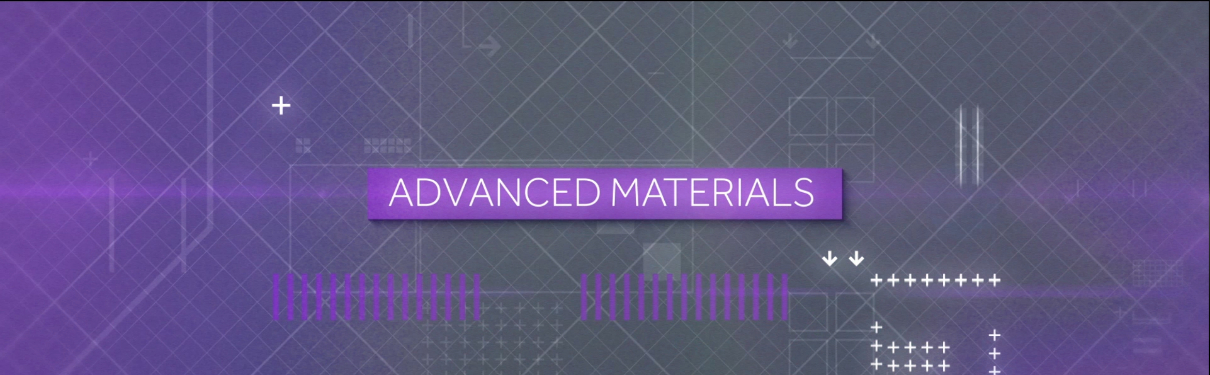
Foreword
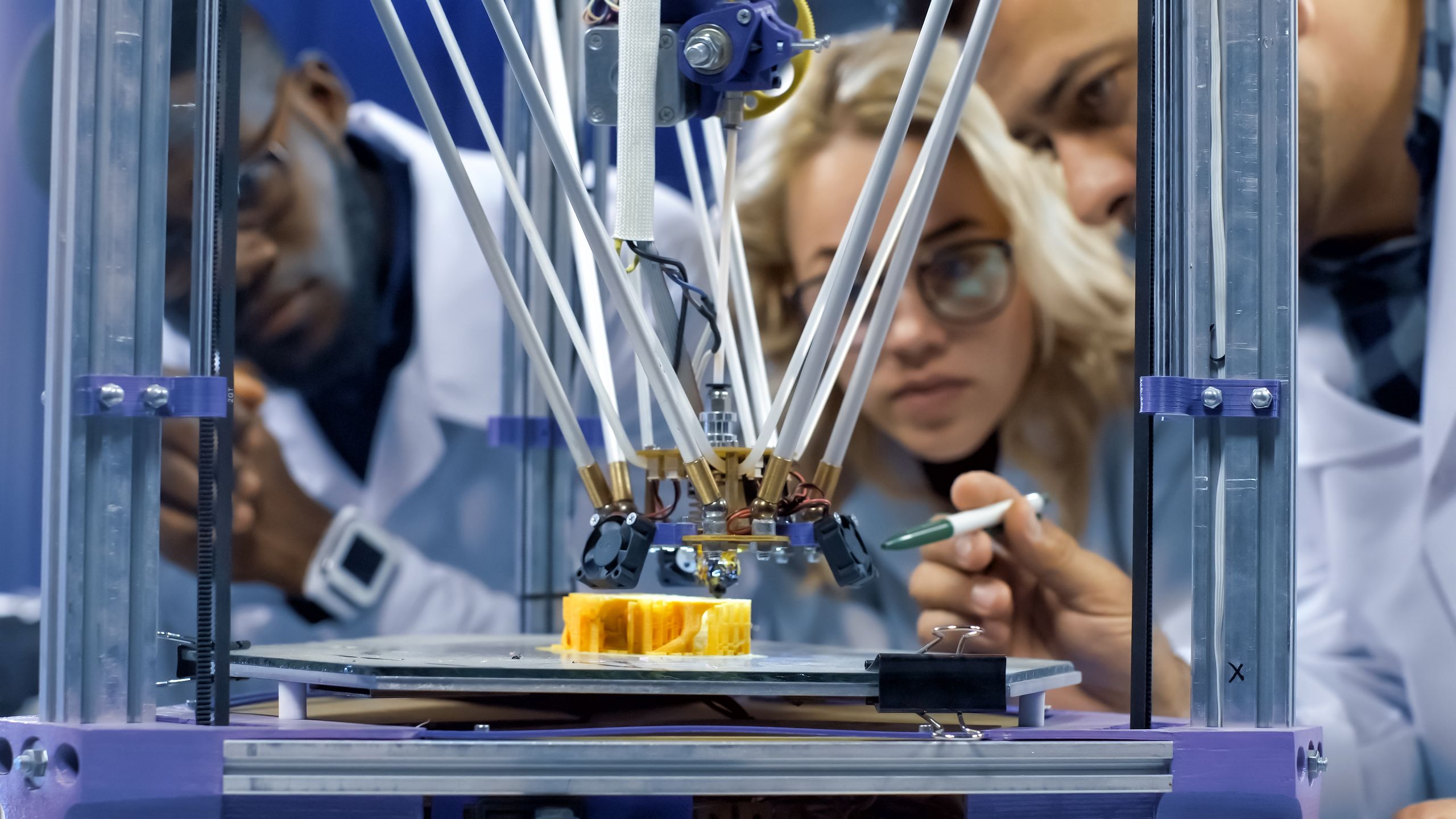
In recent years technology has often been treated synonymously with the intangible activities of the digital domain. Yet, we live in a material world and most of society’s grand challenges have a strong material foundation. For the sustainability challenge, that may lie in reducing the resource costs or pollution effects of materials through the ways in which we source, process and recycle them, or in using new materials to unlock new energy sources, or by reducing energy consumption through lightweighting transport vehicles. In the domain of health, biomaterials offer new ways to repair or replace human body parts, while the search for new supplies of clean water is enhanced by the possibilities of innovative membrane technologies to make desalination and clean-up far more efficient.
The University of Manchester is engaged at the front line of innovation in advanced materials and we are proud to feature the area as one of our five research beacons. Our aim is both to perform breakthrough research and to accelerate the innovation process which will take those insights through to application. Traditionally, new materials have had a very long lead time as incremental innovations seek to combine with complex product cycles and the demands of new processes. Our aim is to transform that process by spanning technology readiness levels in novel ways. The need for standards, regulation and behavioural change help to make effecting these transitions to be as much a challenge for the social sciences as for STEM subjects.
Advanced materials also represent a focus for one of our most powerful instruments, the interdisciplinary research Institute. Our portfolio includes our two flagship graphene buildings, the National Graphene Institute and, closer to business, the Graphene Engineering Innovation Centre. These line up next to the national hub for the Henry Royce Institute for Advance Materials Research, the Manchester Institute for Biotechnology, and coming soon, the Christabel Pankhurst Institute which will bring an interdisciplinary approach to health challenges. In this volume leaders from these Institutes and from our Schools open up a breath-taking range of opportunities while grounding these with the knowledge that can only come from deep expertise. I invite the reader to read these as a key to understanding how the University is working with the city through its Local Industrial Strategy to ensure that Greater Manchester takes its position as a global leader in materials innovation.
Professor Luke Georghiou is the Deputy President and Deputy Vice-Chancellor at The University of Manchester, and is a Professor of Science and Technology Policy and Management in the Manchester Institute of Innovation Research. He has been Chair of the European Universities Association Council for Doctoral Education since 2016.
If any questions arise regarding the research and objectives explored within this publication, Policy@Manchester can help to arrange discussions with the relevant researchers.
If would would like our print version of On Materials, you can download a copy here.
Innovation: why we need to fail more often, in order to succeed
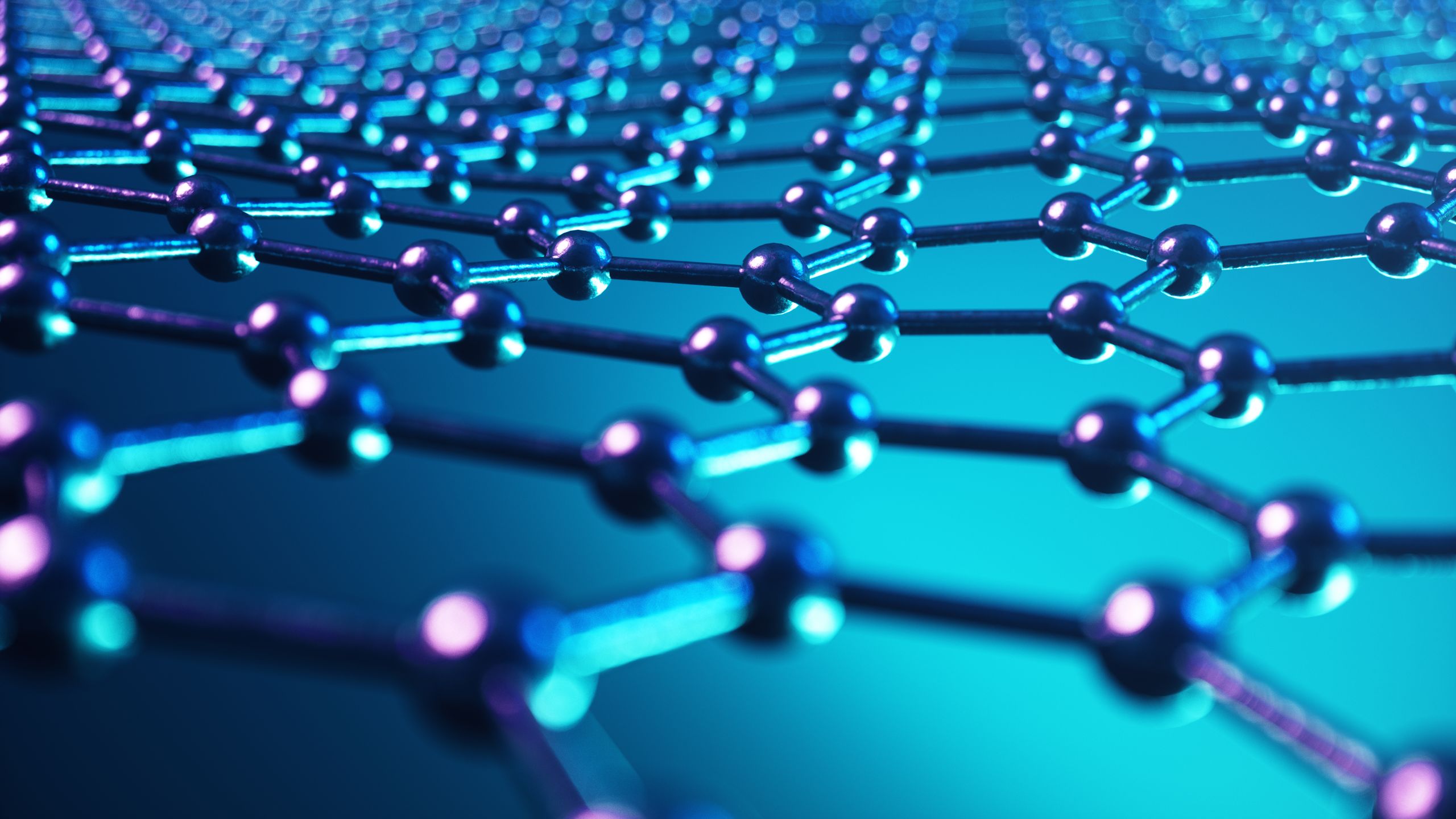
"If I had asked people what they wanted, they would have said faster horses.” This famous quote is often attributed to one of the greatest innovators of all time, Henry Ford. What Ford alludes to is the frustrating truth that customers will default to their known experience and, if asked in the early 1900s what their ideal future transport would be, they would not have chosen his vision for the car.
And here lies one of the great challenges for the global innovation community. How do you choose the metaphorical horse that is most likely to win, in the highly competitive race to deliver the next ‘Big Thing’?
American pioneers and risk takers
In the wake of Henry Ford we have seen North America produce a succession of brave and determined pioneers who have delivered highly disruptive products and services such as visionary Steve Jobs at Apple, Jeff Bezos the founder of Amazon, and Elon Musk, the technology entrepreneur behind the Tesla electric car. The big breakthrough for Apple was the iconic Macintosh in 1984, the first affordable computer with a graphical interface which was to change the world of publishing forever. And the pace of innovation has continued with the launch of the iMac, the iPhone and iTunes, all of which revolutionised the communications, technology and music industries. While these ground-breaking innovations were massively successful, as Steve Jobs said: “Sometimes when you innovate, you make mistakes. It is best to admit them quickly and get on with improving your other innovations.”
Strategy, structure, and the UK approach
The UK approach to innovation is a little different. In recent years we have seen more large scale public-private sector partnerships – and to help pick the winning horse the government has created sophisticated frameworks like the Industrial Strategy. This carefully selects the grand challenges of the future, such as harnessing the power of artificial intelligence (AI), driving new developments in mobility and transport, as well growing our economies while also safeguarding our environment.
I applaud this strategic approach, as it enables the UK economy to apply its resources in a focused way, bringing huge economies of scale and delivering commercially supported solutions that also benefit the wider good. A great example is the Faraday Institution which is looking to radically develop the UK’s capability in battery technology. This ambitious university-business partnership has been funded in part through the government’s £246 million investment in battery technology. It aims to make the UK the go-to place for the research, development, scale-up and industrialisation of cutting-edge battery technology. For me, the real value of the Faraday Institution will be establishing a pipeline of focused, substantial, and managed research projects in areas defined by industry, but delivered by businesses and universities, working in partnership.
The right model for advanced materials?
This classic sequential approach reminds me of the so-called ‘waterfall model’ which originated from the construction industry and was later adopted by computer programmers. Development is essentially segregated into a sequence of pre-defined phases, including feasibility, planning, design, build, test, production, and support. However, for me this may not be the best approach to deliver innovation when it comes to advanced materials which I believe will deliver the most disruptive underpinning technologies of our time. The fast pace of development in this exciting field means it’s perhaps too difficult to forecast an ultimate winner – instead, like those US pioneers, let’s start the race and see where it takes us.
Fail fast, learn fast
The clock is ticking. A range of sectors – including automotive, aerospace and construction – are impatient for the innovation they need to be sustainable, both economically and environmentally. A new generation of advanced materials are the most likely candidates to make the necessary difference to these businesses.
I also believe that we can accelerate innovation without compromising safety, thanks to the advent of increased digitalisation in the industrial and manufacturing sectors - for example, adopting sophisticated modelling techniques, such as digital twin technology, to replicate ideas and quickly help identify and reduce potential risks.
To meet this demand a more agile, ‘fail fast, learn fast’ approach needs to be adopted across the advanced materials innovation community. This method focuses on short-term pilot projects and echoes the advice from Steve Jobs on being prepared to make mistakes, admit them quickly and get on with improving the innovation. It departs radically from the mainstream innovation model, because rather than trying to pick (and spend time and money) on a potential winner, we could instead spend much less time on running say, ten plausible projects all at the same time, but at a much earlier stage of their development. As we learn from our failures, we select or combine innovations that look to be winners.
The productivity puzzle
It all feels counter-intuitive but by making these informed quick-steps, the innovation journey should progress at a faster pace – and without the burden of the huge R&D investment normally required to develop a perfect, risk-free solution at every stage. This agility and speed to market would also improve productivity - perhaps the biggest drag on our economy.
The UK has experienced a slump in productivity growth since the financial crisis that shows no sign of ending. As a report by the Greater Manchester Independent Prosperity Review explains: “Almost every advanced economy has seen a sharp slowdown in productivity in the last decade. However, the UK has been amongst the most affected, and the gap with competing economies is getting wider. The UK’s output per hour is 76% of that of the US, 78% of the French, and 79% of Germany [...] research by the Office for National Statistics (ONS) highlights a decade of stagnation, with UK output per hour not that significantly different to the level in 2007. This slowdown is often referred to as ‘the productivity puzzle’.”
How do we solve this puzzle? Well, I believe we should be looking at more agile innovation in the various organisations and institutions that support our economies. A special report produced by business thought leader Raconteur and published in The Times newspaper earlier this year highlighted the role of the supply chain in providing leadership in delivering innovation. As well as adopting new technologies, the Supply Chain Innovation report highlighted the need for more agility and collaboration across supply networks. Malcolm Harrison, Chief Executive of the Chartered Institute of Procurement and Supply, said: “If an agile and flexible approach can be fostered without too much fear of breaking with the norm, an organisation can respond much quicker when innovations are presented, reaping the benefits fast and without having to wade through layers of process. This can become a competitive advantage.” And this is where The University of Manchester’s lab-to-market model comes to the fore.
The Manchester model
The ‘fail fast, learn fast’ approach should work well for the model innovation community now being led by Manchester, which features a ‘science supply chain’ that runs seamlessly across academia and commercial end-users. For us, this journey begins in research groups based in the University and where blue sky thinking can be nurtured in centres of excellence like the National Graphene Institute (NGI).
When the science is mature enough, we can transition it into projects based in the nearby business-facing Graphene Engineering Innovation Centre (GEIC). The GEIC proactively engages with business partners for whom 2D materials could prove transformational, including lightweighting, energy storage and membrane technology. For example, innovations to ensure your battery-driven car of the future is no heavier than the fossil fuel-powered vehicle it replaces, or your children and your children’s children will access sustainable energy and clean drinking water, regardless of the climatic conditions to come.
These flagship facilities are also part of a wider innovation eco-system including the Henry Royce Institute as well as Manchester’s Graphene City, an innovation ecosystem featuring a critical mass of scientists, manufacturers, engineers, innovators and industrialists centred around fully integrated lab-to-market capability. This unique advanced materials community will also contribute to the broader vision of ID Manchester - an ambitious scheme that will regenerate the University’s north campus to provide a 26-acre site that will be home to a new Innovation District in the heart of the city. The aim of this university-led project is to nurture a world-class community based around collaboration and enterprise. As the go-to place to discover disruptive technologies and creative thinking it would be an ideal place for ambitious start-ups looking to scale up or an international business wanting to establish a UK HQ. This £1.5 billion project has the potential to create over 6,000 new jobs – some of which, I have no doubt, will require highly skilled people who can work in the new 2D materials economy.
The catalytic role of Graphene City has been highlighted in the Greater Manchester Independent Prosperity Review which identifies innovation and the role of universities as a key driver to boosting regional UK productivity, stating: “...when it comes to the links between universities and business, there should be a role for strengthening the outstanding capabilities in basic research, idea generation and invention, as typified by Graphene City, as well as growing ‘incentives’ for the application of university research results. Here, incentives for increased R&D spending by firms and larger outlays for the purpose by Government should be a priority. The links to the Challenges identified in the Government’s Industrial Strategy and the respective opportunities for growth are key.”
Less fear, more entrepreneurial spirit
It’s important to recognise that the ‘science supply chain’ will not necessarily always mean a smooth transition from lab to market. A project could hit a setback at any stage and have to retrace its steps as the problem is unpicked and looked at again (like that frustrating moment in a game of snakes-and-ladders). This, however, is the potential strength of the Manchester materials model because by responding quickly to failure we can fast-track science-to-product innovation.
So, what I would encourage national policymakers and public funding bodies to think about is this - failure is nothing to fear – if it’s managed in the proper way. A losing horse one day could be a champion a little bit down the line, if nurtured in the proper environment. Innovation is the same.
Creating an innovation community is also just as critical to facilitate this more entrepreneurial approach. This massively mitigates the risk, but it does require infrastructure (research and scale-up facilities, a supporting supply chain, digital tools, etc) and people (bold leaders from academia and the business world, skilled professional staff, and world-class researchers).
If we are to remain competitive at a global level, the UK’s strategic innovation community, led by the Department for Business, Energy and the Industry Strategy (BEIS), must not lose sight of the value of true entrepreneurial spirit, while working toward objectives set by the Industry Strategy and all its ambitious planning, consultative workshops and competitions. In a speech delivered in September 2012, one of the early architects of the nation’s economic plan, the then Business Secretary the Rt Hon Dr Vince Cable, stated that “a good industrial strategy allows for failures, and recognises that innovation may strike in an unpredictable place”.
So, what would I recommend the UK’s strategic innovation community to consider in their plans?
- The need to have an ‘innovation stream’ within the Industry Strategy Challenge Fund that introduces and adopts the ‘fail fast, learn fast’ approach.
- A cultural shift in national funding and policy thinking with a recognition that the UK should be nurturing innovation winners based on the ‘fail fast, learn fast’ approach and not just ‘picking winners’.
- The need to identify and support exemplar innovation eco-systems that enable the ‘fail fast, learn fast’ way to innovation (Graphene City would be a good example).
Our economy, our daily lives and our planet stands to gain, and the sooner we start, the sooner we’ll reap the benefits.
James Baker is the CEO of Graphene@Manchester at The University of Manchester.
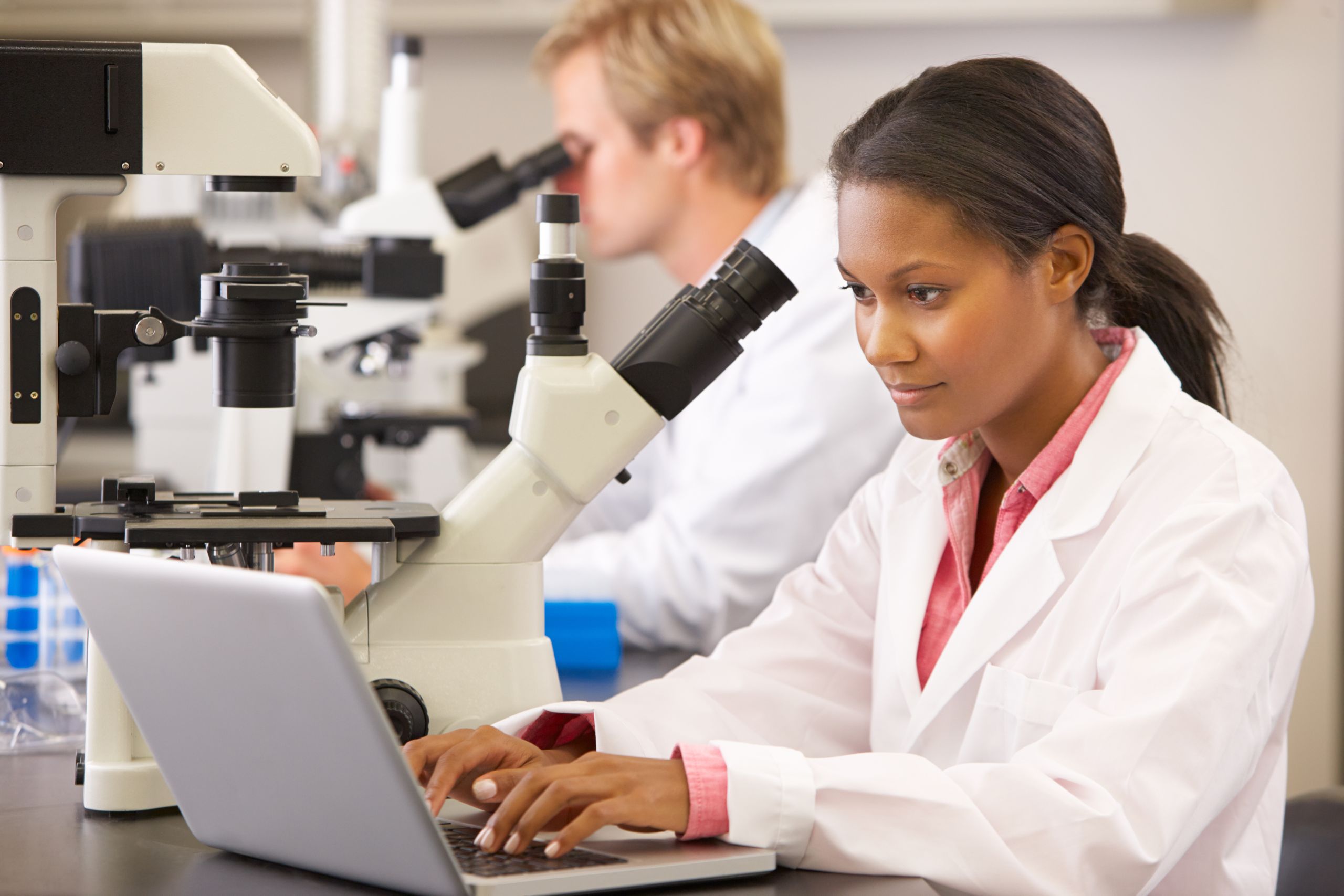
Biomaterials: how can we get from the lab to the patient sooner, and more easily?

Biomaterials are integral to a huge number of medical technologies. These are the advanced materials introduced into our bodies: artificial hips, bone grafts, heart valves, pacemakers, catheters, stents, enamels, fillings and many more medical devices contain highly-specialised biomaterials. With a rapidly growing and ageing population, the UK healthcare system needs to make the best possible use of biomaterials to provide cost-effective interventions that will help to meet this challenge. But why does it take so long to get from lab to patient, and what’s holding us back?
Research success vs commercial success
The global market for biomaterials is estimated to be worth $70 billion (2016) and is expected to grow to $149 billion by 2021. Within the UK, the medical technology sector has doubled since 2009; it is the sixth largest in the world and third largest in Europe, with a turnover of £21 billion per year.
However, while the UK is extremely successful in the development of these materials, it is less so when it comes to getting these translated quickly into products available for use. In the Times Higher Education World University Rankings, UK universities rank first and second worldwide in Research (which measures research volume, income and reputation); but the highest UK ranking in Impact in Industry, Innovation and Infrastructure, which focuses on universities’ role of fostering innovation and serving the needs of industry, is 11th. This was highlighted to us just last year by Dr Edward Draper, the Chief Executive Officer of Ortheia, at the SME accelerator day at the Henry Royce Institute.
The knowledge gap and new innovations in Manchester
A major contributor to this lack of success has, I believe, been insufficient knowledge of the stringent regulatory requirements necessary to get new biomaterials from the laboratory to the clinic, ensuring patient safety. Within The University of Manchester, this issue has been recognised and steps are being taken to tackle it, with teams taking exciting new biomaterials ideas into clinics and commercial ventures. This includes new materials to treat nerve damage, peptide based hydrogels for cell culture and colloid gels designed to treat chronic back pain resulting from disc degeneration.
The University of Manchester’s Professor of Biomaterials, Julie Gough, and Dr Adam Reid, a senior Clinical Lecturer in Plastic and Reconstructive Surgery, provide one example of this. They have developed a pioneering new treatment for peripheral nerve damage resulting from traumatic physical injury, where standard surgical techniques prove unsuccessful. Their innovative solution is the development of Polynerve, a biodegradable polymer nerve conduit (a kind of bandage to aid healing). This is essentially a small tube attached to either end of the severed nerve, designed to aid the healing by guiding the re-growing nerve, while breaking down and being absorbed by the body during this process. Although the concept of nerve conduits is not new, techniques developed by Professor Gough have been able to create a microgroove patterning on the internal surface of the conduit, which was previously not possible. Research conducted by Professor Gough and Dr Reid have shown that these microgrooves provide tracks, which guide the re-growing nerve cells across the ‘nerve gap’ between the severed ends of the damaged nerve, accelerating repair. Polynerve is currently being used to treat 17 patients in a Phase I clinical trial in Manchester, which will determine its safety and efficacy of the micro-grooved conduit.
Vital learning & new ventures
Through the course of this work, Professor Gough and Dr Reid learned what is required to safely translate a truly innovative idea from a proof of concept and discovery in the laboratory, to determining whether this idea improves patient outcome. This is a complex process, comprised of multiple stages designed to ensure patient safety at every step of the manufacturing and treatment process, requiring specialist knowledge of the material, its manufacture, the surgical techniques required to utilise it and the legal framework determined by the government to protect patients. This knowledge, often the domain of specialised departments of large enterprises, will now aid other teams at the University involved in biomaterials’ innovation. I have been working with Dr Jason Wong, Senior Clinical Lecturer in Plastic and Reconstructive Surgery, towards the translation of a fibrous degradable innovation for tendon repair techniques, which augments current suture repair techniques of damaged tendons by aiding cellular regrowth and guiding extracellular matrix deposition. With these innovations, we have identified that other opportunities arise to engineer new enabling surgical tools that facilitate safer and more efficient surgery. This work is now being supported by the charity, Versus Arthritis, to develop new ways to introduce biomaterials into everyday surgical use.
Outside of the University, biomaterials developed in Manchester have also been taken from lab to products that are getting close to market spun out into SMEs, with the help of commercial investment. Professors Tony Freemont and Brian Saunders together have developed a gel designed to treat chronic lower back pain resulting from degeneration of the intervertebral disc, by providing support to damaged discs. This gel is being developed by an SME called Gelmetix and is expected to enter clinical trials this year.
Outside the strict regulatory requirements of clinical trials, Professors Alberto Saiani and Aline Miller, through their company Manchester BIOGEL, are developing fully synthetic gels which are making it possible to gain a more accurate understanding of fundamental cellular function in mammals. Composed of small, simple protein components that capture individual water molecules, they give rise to a jelly like substance of varying stiffness. These fully synthetic gels, are improving the current methods of cell culture and enabling biologists to grow cells in environments that mimic the physical conditions of our bodies much more closely. When compared to standard cell culture techniques, where cells are grown on hard plastic in two dimensions, conditions they are not likely to encounter, these gels enable biologists to gain a level of understanding about cellular function, which would not be possible through standard two-dimensional culture methods. This enhanced understanding, opens up the development of new cell-based therapies and the next generation of targeted drugs.
Professors Saiani and Miller have successfully translated their discoveries into a commercial enterprise which will make their revolutionary new product available to researchers, not only in Manchester, but across the UK and internationally.
Regulation and the need for change
While there are examples of success, we are still not consistently enough translating innovative biomaterials into commercial and clinical products. A major contributor to this lack of success is a deficit of knowledge surrounding the complex regulatory environment required to ensure patient safety.
Part of the problem is a lack of understanding of the cost associated with the regulatory framework surrounding medical technologies. A new EU medical device regulation comes into effect in 2020. This aims to enhance the safety of new medical devices by requiring a Unique Device Identification System for all devices used on patients (which now includes medical software), and the approval of an expert regulatory qualified person within the organisation developing it. Practically, whilst enhancing patient safety, this regulation will make it more expensive for SMEs or academic manufacturers to produce innovative products for use within the EU. In his work on the development of Polynerve, Dr Reid also found that beyond a lack of regulatory expertise, the ability of academic institutions to engage with companies on post-manufacturing processes, such as sterilisation, packaging and distribution at grant-affordable costs, has proved a barrier to successfully getting new material-based medical technologies to market. During this project it was also found that the cost of regulatory advice is high while the quality of the advice is very mixed, with no clear standards adhered to.
Given these challenges, we need to:
- Address the knowledge gap on regulations and how the process works by ensuring it’s included in PhD training programmes.
- Encourage regulators such as the Medicines and Healthcare products Regulatory Agency (MHRA), European Medicines Agency (EMA) and the Food and Drug Administration (FDA) to understand that this knowledge exchange is a two-way street, making changes where necessary to how the regulatory environment is explained and presented, ensuring there are no unintended barriers to innovation. MHRA staff have a duty to patient safety and need to facilitate promising technologies, while weeding out those which are least impactful.
- Engage the end users of the technology, both at the clinician and patient level. Clinicians need to guide the R&D process, with continual input from patients from the outset, as there are many barriers to getting a product right that cannot be addressed by focusing only from a regulatory stand point. We must always address patient and unmet clinical need, not just focus on the push of new technologies.
Collectively, with some changes at both the level of the regulator and the researcher, and with input from both patients and clinicians, the biomaterials sector has a great opportunity for increased productivity, leading to more innovations and greater benefit for patients.
Professor Sarah Cartmell joined The University of Manchester in 2010 and has been a Professor of Bioengineering since 2014. She also works in the School of Materials as the Deputy Head and the Head of the Biomaterials Group.
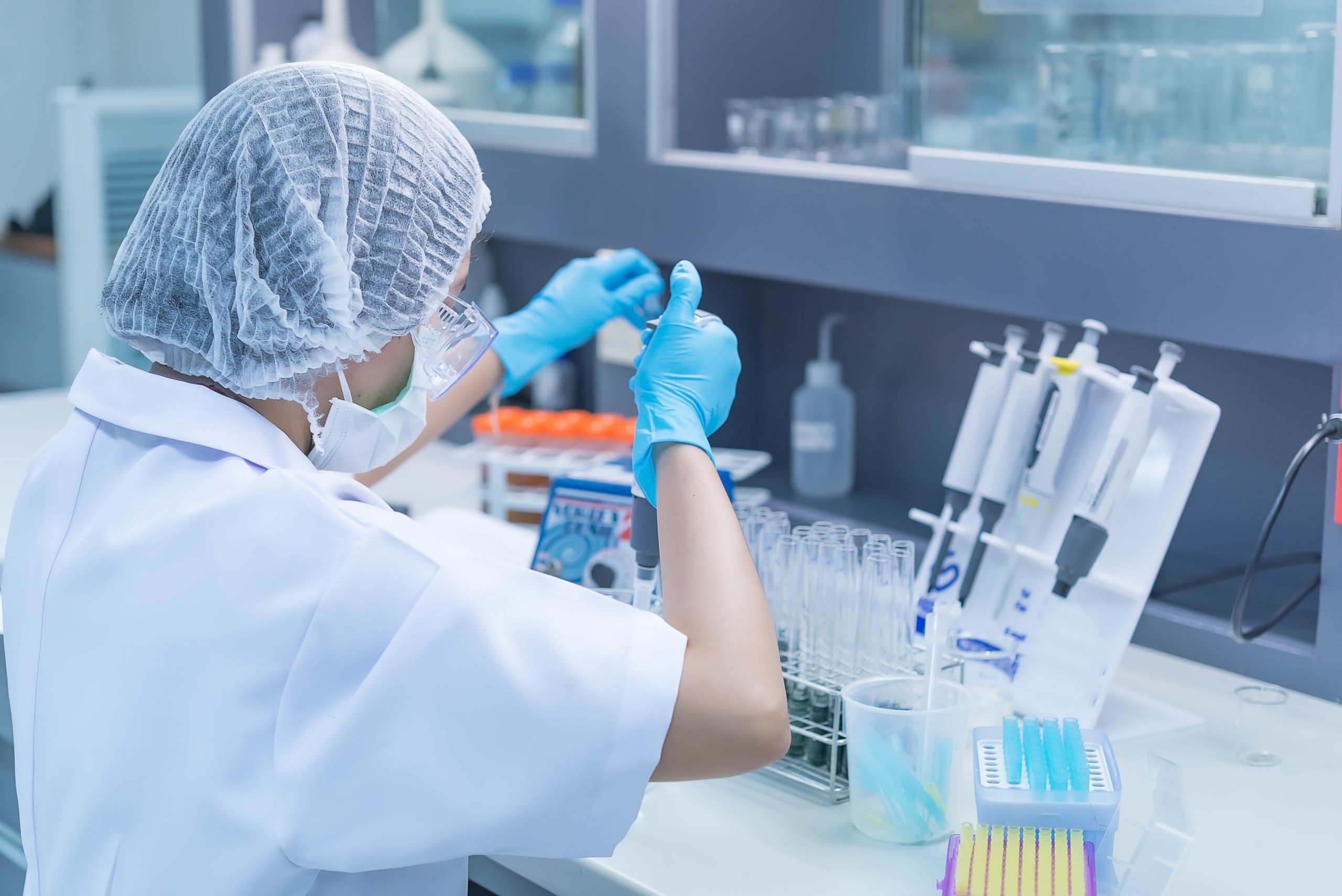
Science, industry, and government must pull together to solve our plastic addiction
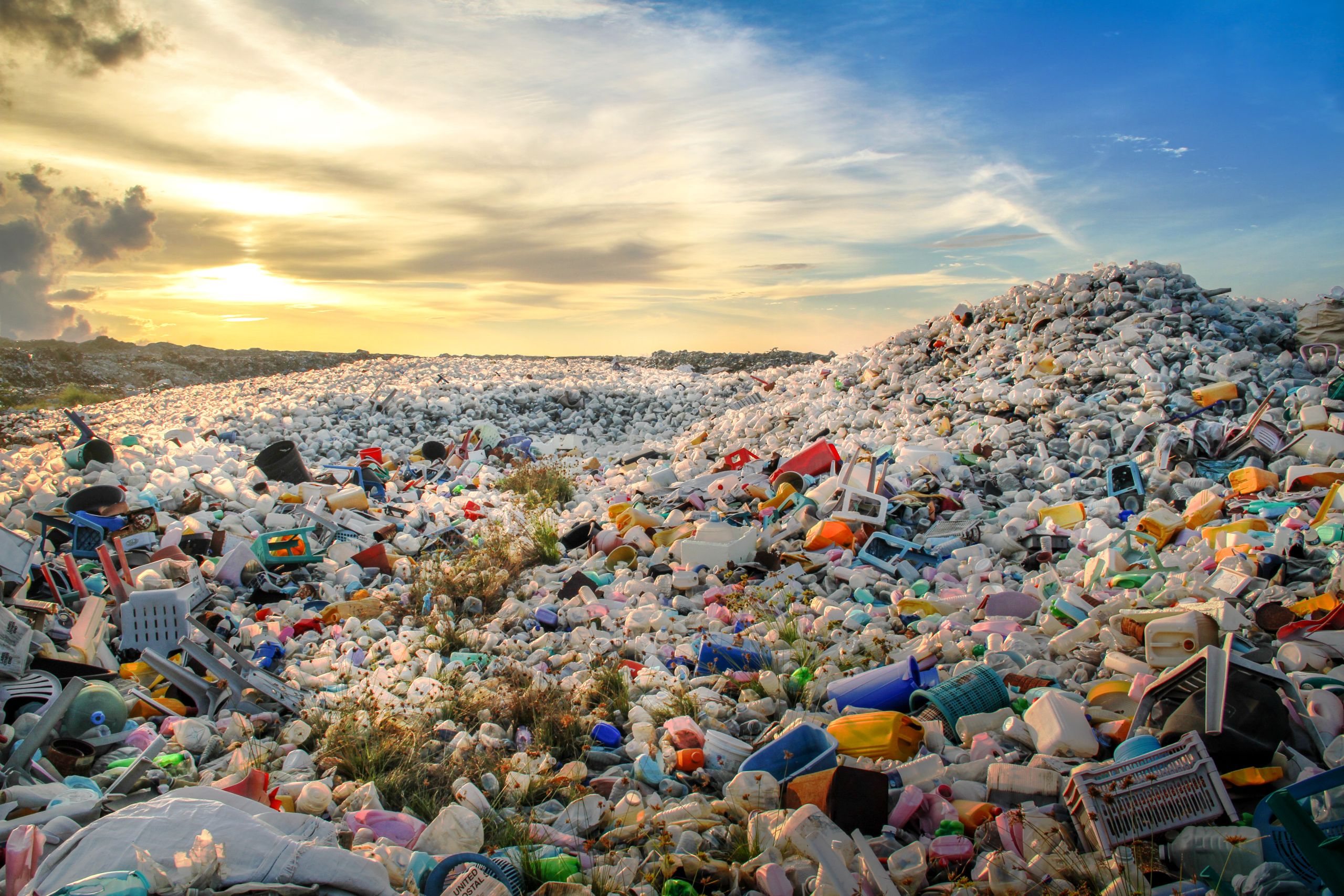
As a society we have a problem - like it or not, we’re addicted to plastic. And it’s not hard to understand why. Plastics are miraculous materials - a remarkable 20th century invention which has changed our world. From Lego bricks to heart valves, from toothbrushes to computers, plastic has countless practical uses. But what was once hailed as a wonder material is now widely viewed as an environmental scourge of the planet. So how should we view this most astonishing and prolific material and more importantly, how can we solve the problem we’ve created?
Plastics have provided massive energy savings compared to the many materials it has replaced during the last 50 years: lighter cars that burn less fuel, food that lasts longer on shop shelves, packaging that weighs less, windows that better insulate your home - plastics have revolutionised supply chains across practically all industries. And yet it’s the poster child for the wasteful take-make-dispose linear economy. A lot of that is to do with the fact that every single piece of plastic that has ever been produced is either still with us somewhere, in your kitchen cupboard, in a landfill site or floating somewhere in the oceans. Or, if it has been incinerated, it’s released its entrapped carbon as the greenhouse gas, CO2.
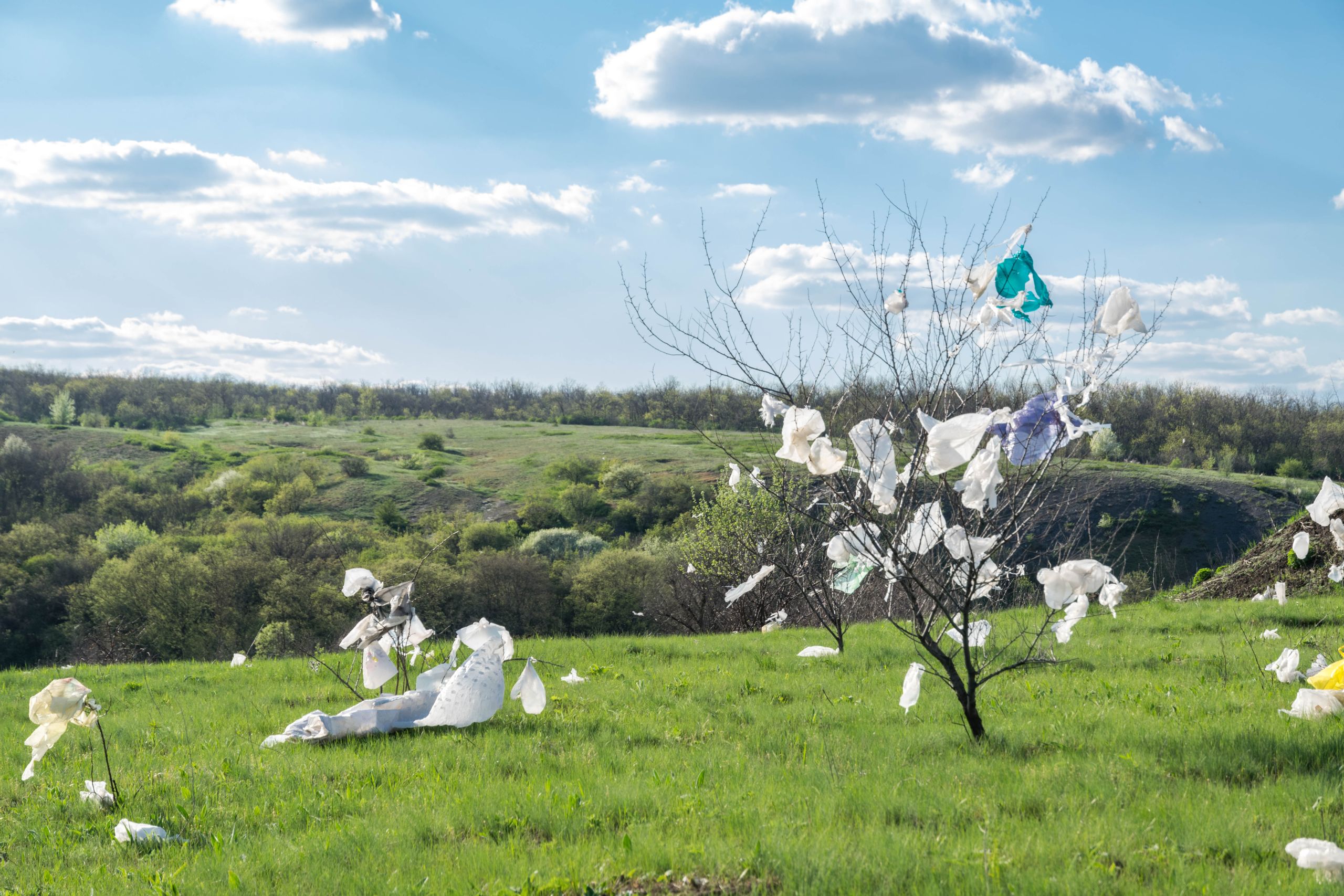
Thoughtful sustainability?
So how might we design alternative materials that fit our lifestyles, economy, and needs without such environmental damage? And how can we create a regulatory environment that incentivises genuinely sustainable innovation and avoids putting barriers in the way of getting solutions rolled out?
Sustainable advanced materials need thoughtful analysis of the whole material life cycle to address present and future challenges. We need to be clear on how the product is being made, the cost of that process, what the final product is actually going to be used for, and most pressingly, what will happen to the product when it’s reached the end of its ‘life’; things that perhaps weren’t given much thought, at the start of the 20th century, when plastics were the ‘advanced materials’ of their time.
BBC Television’s Blue Planet II highlighted the problem of single-use plastic packaging, but when people talk of wanting a ‘plastic ban’ it’s important to realise that plastics in particular are pervasive and impact every aspect of our lives, because of their incredible versatility. Trying to find a replacement material that can do all the same things as plastic is impossible – there is no one silver bullet that can solve our plastic problems – and solutions often do more hidden environmental damage than good. Blanket bans are foolish and overly simplistic - microbeads in personal care products are fine if they degrade - but degradation needs to be proven in real environments. Demonstrating that a material can degrade in a controlled solution isn’t the same as showing it can do so in a fatberg-infested sewer.
Solutions and quick wins
And so, the solutions must be product specific. What is the best solution for all the different waste challenges we face? While it is perilous to replace all of our plastics with biodegradable alternatives due to the unknown ecological risks and loss of arable land, there are some quick wins.
Plastic films that are challenging to recycle, such as those found at the top of meat packaging or fruit punnets, are an excellent target for biodegradable plastics, as are many sources of microplastics found in cosmetics or from washing textiles. Conversely, hard plastic containers can often be recycled well, and so we should focus here on smartening our recycling infrastructure and encouraging reuse. The key is to efficiently make this waste worth something – to give it a value, regardless of its origin, which means that different solutions are needed for each plastic challenge. The plastic legacy isn’t going to disappear from a whole suite of alternatives, but from a combined approach of innovation in advanced materials alongside innovation in how we recycle and manage our waste.
Recycling rates in the UK and the rest of the world are far short of where they could, and I’d argue, should be. This individual and infrastructural laziness has been compounded by China’s decision to stop accepting all the contaminated recyclable materials that most of the Western world has been sending them. This is forcing us to finally fix these problems ourselves and will hopefully lead to innovation, both in policy and in solutions, such as the development of optical sorting, where cameras or lasers sort our solid waste matter for us.
We must urgently develop technology and infrastructure for companies or public authorities to profit from and properly collect 'end-of-life' products and materials. Simple policy interventions can help with that, whether it’s ensuring local authorities can all recycle the same materials, or simply that they all use the same colours for recycling bins.
Science and industry
A big part of getting to these solutions, is the problem of scale. There are lots of inventions and processes that are being done on a laboratory scale, but the problem of plastics is huge. And while there are companies interested in these potential solutions, scaling up from a lab experiment to a marketable product is a massive challenge.
The University of Manchester is quite progressive in its approach to bridging this gap – for example, the Graphene Engineering Innovation Centre (GEIC) is bringing industry into the University to work closely with academics to help scale up pilot projects to market, while the Royce Institute is bridging the materials science gap in a similar way. This leadership is built on exceptional research efforts, including Dr Arthur Garforth’s development of catalysts for waste valorisation, the Sustainable Consumption Institute’s recognition of the societal factors that impact decision making around plastic packaging use or work in our own group on fast-degradable polymers using designer monomers - new molecules that work together to mimic polystyrene packaging.
A more collaborative future
So where do we go from here? We clearly need policy decisions to be joined up with the science that underpins our understanding. Simplifying our recycling systems will greatly improve personal compliance. We need experts who can work comfortably across disciplines, versed not only in materials science decisions, but also in the social science understanding of how the complex industry supply chain and public consumer will interact with these materials. The RE3 research project led by The University of Manchester brings together manufacturing, social, and material scientists, and several other academic and industrial partners. Among other things, this project is looking at demonstrating new methods for recycling soft and mixed plastics and non-plastic films, and creating smart circular economies that allow users to take ownership of and reduce plastic waste.
We need a unified understanding of what terms mean – compostable does not mean biodegradable, and biodegradable in a lab does not mean biodegradable in a sewer or the ocean – preferably underpinned by proper metrics. This will help shape a future where the best academic research is developed in collaboration with industry partners from across the supply chain, underpinned by funding from government to translate new ideas, like The University of Manchester work I’ve described here, into scalable solutions.
Most importantly, all developments should be based on rigorous and robust science, utterly transparent and accountable, and follow through any new solutions to their own ‘end-of-life’, otherwise we risk creating new problems for future generations.
Academics, industry, waste managers and government regulators must start pulling in the same direction to solve this grand challenge.
And if there’s one thing we can’t waste, it’s time.
Professor Mike Shaver is a Professor of Polymer Science at The University of Manchester's School of Materials. He also leads the Green Materials Laboratory developing biodegradable materials.
Advanced materials and electricity: the power to help save the world?
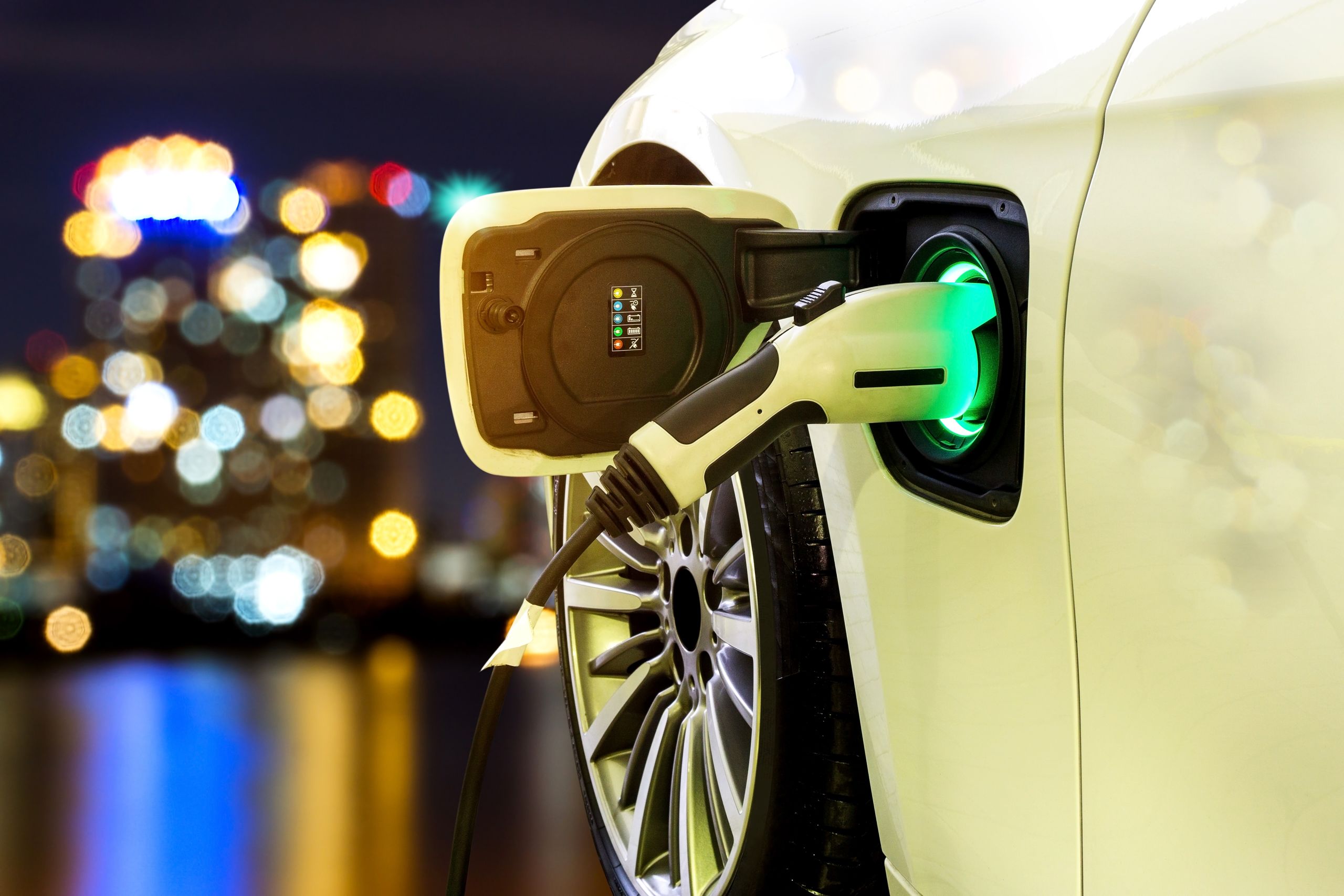
Advanced materials are my favourite kind of materials. Why? Because I believe they could help dramatically improve our world. We already use many in high-tech applications: aircraft engines use blended metals known as metallic superalloys; computer chips use ultra-thin, nano-scale silicon wafers; and smartphones use chemically-strengthened glass. Smashing! (Or rather not).
All these materials were developed and applied to address specific technical issues; we need something stronger, thinner, less corrosive, and so on. They enabled globally transformative technologies, ones with great socio-economic benefits.
But the world now needs us to develop transformative technologies with a difference. Not for cheaper air travel or larger media networks, but to stave off an environmental catastrophe which threatens the existence of our civilisation.
Battery powered
My day job is to look at how advanced materials can be used to improve electrochemical energy storage devices – in other words things that store electricity, like batteries and supercapacitors, which I do at the Graphene Engineering Innovation Centre (GEIC). From hearing aids to cars, wrist watches to laptops, batteries are everywhere, and our world relies on them.
Advanced materials, such as silicon nanoparticles, may be able to increase the power of a battery by roughly one third which makes them more efficient; however, these types of batteries can degrade rapidly. Use of 2D materials, such as graphene, can prevent degradation while maintaining battery life; in other words, you can use and charge your battery many more times before it starts to degrade and needs to be disposed of, which is better for our environment too.
Another challenge with traditional batteries is they can catch fire. This happens more often than you might think and is usually due to internal short-circuits creating high temperatures and igniting the flammable electrolyte. Fusing other 2D materials into specific battery components could prevent many common causes of battery fires.
Towards electricity, away from CO2
My aim is to enable technologies at many scales, from biomedical implants with micro-batteries (think pacemakers and vital sign monitoring), to renewable energy storage with giga-batteries (something the size of a few houses). However, one of the most important technologies advanced energy storage materials will transform, is that used for electric vehicles (EVs).
Have you ridden in a car recently? Did you know that even the ‘greenest’ petrol or diesel cars produce a minimum of 1kg of CO2 every 10km? That’s 1kg of CO2 just from driving a few miles, from the M60 ring road to Manchester city centre. Every day, people in Greater Manchester travel roughly 1.4 billion km in their cars. Even if everyone were driving the ‘greenest’ car (which they most certainly are not) that’s around 140,000 tons of CO2 spewed out daily. But it doesn’t stop there. Those figures are for light duty vehicles alone. What about the heavy haulage industry, the shipping industry and the airline industry? These are all massive markets containing transport vehicles powered by fossil fuels. We need to electrify all of this, but the technology isn’t there yet.
The answer to the problem of our road transport being utterly reliant on fossil fuels, is modern EVs. First developed in the late 1800s, EVs were actually here before their fossil-fuelled counterparts, but due to improvements in internal combustion technologies, they were overtaken by the petrol and diesel vehicles that dominate today. A new breed of EV appeared at the turn of the century. The latest incarnations of these have ranges up to 300 miles (and soon beyond) and can fast charge up to 80% in 15 minutes. Yet compared to the actual number of petrol and diesel cars on our roads, EVs are still just a drop in the ocean. UK electric vehicles made up just over 2% of new car sales in the 12 months to September 2018, compared to Norway where over the same period, 47% of all new vehicle sales were plug-in electric.
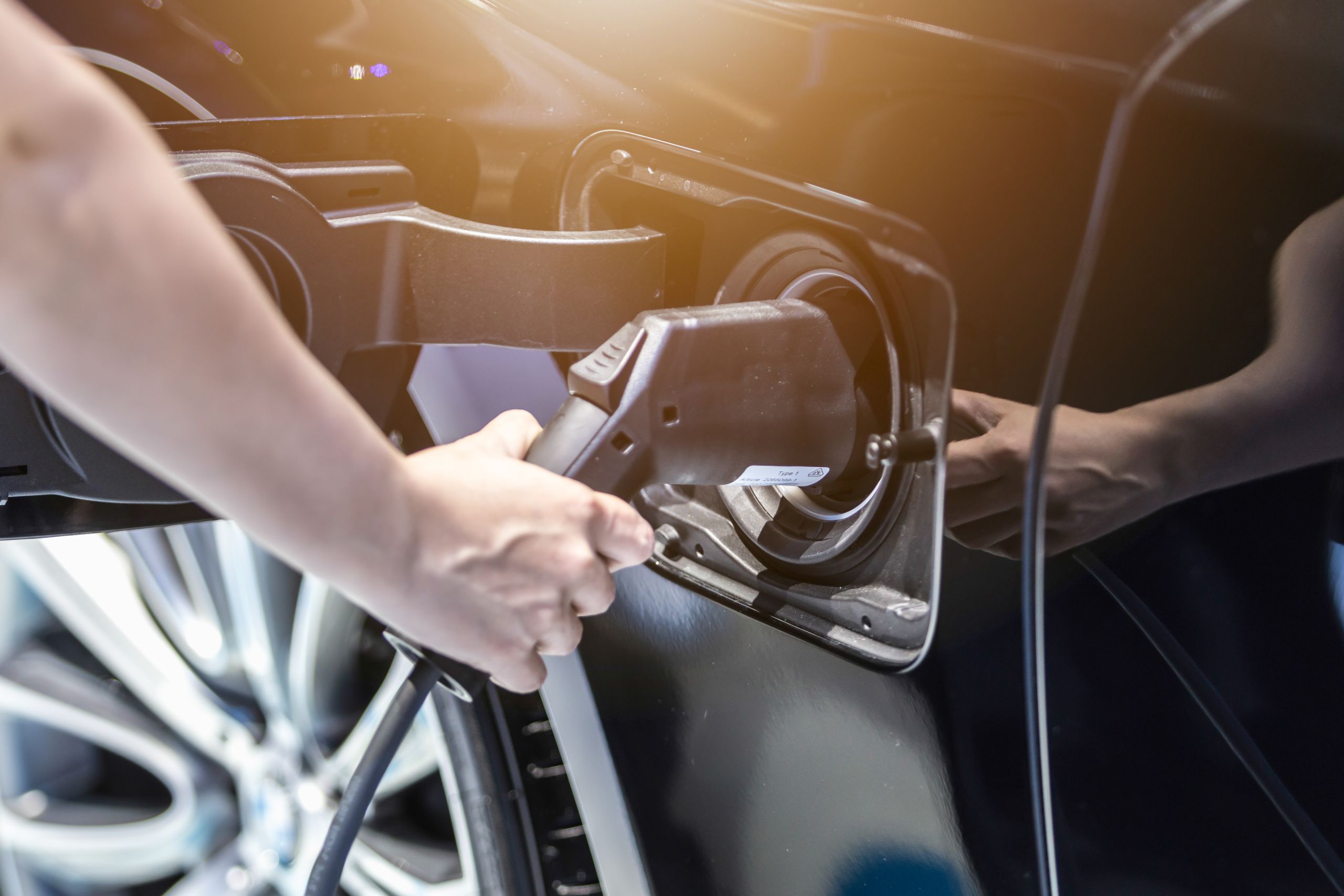
The race for better batteries
So how can we encourage greater take up of EVs? We have batteries with the energy density to power long-haul trucks (500 miles+), but they currently degrade significantly after a few journeys. We also have energy-storing supercapacitors which can be fully recharged in a few minutes, but currently only provide a 20 mile range for an electric car.
It’s clear, then, that to electrify all the vehicles that we rely on day to day, we need better batteries, and according to the Intergovernmental Panel on Climate Change (IPCC) assessment report, we need them within 12 years. This may sound like a long time, but traditional research programmes last three of four years – meaning we have only three rounds of these before we need solutions in place (and that takes time as well).
So, there is a need to accelerate not only the research, but also the design and implementation of these technologies. We need new, more dynamic research strategies, where working closely with innovation accelerators and industrial partners is the norm, while retaining some flexibility for pursuing answers to more esoteric questions. We must also not be afraid to adopt modern high-throughput analysis techniques, ones which replace traditional lab techniques with automated systems, combined with intelligent (possibly artificial) decision making on where to go next.
Futuristic visions and machine-based decisions?
Through this approach, perhaps the next advanced material in energy storage may not be ‘discovered’ by a person at all, but instead by a purpose built R&D machine. Imagine if this advanced material was automatically assessed for commercial viability based upon industry costs, performance and environmental trade-offs? Approaches like this would accelerate the discovery and adoption of advanced materials and is the kind of exciting new area that I believe an initiative like the forthcoming Henry Royce Institute will be well placed to explore.
But what can we do now? I’d argue we have the power to make great strides with current technologies. Why do we need a massive two-ton vehicle for transporting one person around a congested city? Couldn’t we, in theory, convert some roads, for example the M60 ring road, into a car park where people transition from long-range, slow-recharge vehicles to short-range, fast-recharge ones, depending on their destination? Imagine if these vehicles could be automatically moved (on tracks?) around the ring-road to where the user enters or leaves the city.
Next steps in the move towards electric vehicles
As great as my vision sounds, maybe it’s a little too bold. Perhaps we can start by recognising that Greater Manchester has just 150 EV charging points, of which 12 are on The University of Manchester campus. If we’re aiming for hundreds of thousands of EVs, 150 charging points is far short of the mark. Perhaps we need to incentivise their use by making the charging point an attraction in its own right, a new economic centre. We could include a range of 15 to 60 minute experiences (virtual reality anyone?), something which can create high value jobs, supports Manchester’s Digital Strategy and kick-starts a new age global business, all made in Manchester.
In the meantime, what should policymakers consider? Some electric vehicles currently benefit from capital subsidies and lower fuel and vehicle taxation. These subsidies will be phased out in the long run as electric vehicles become comparable in price to petrol and diesel cars. And, to ensure the UK is in the top tier of countries promoting EVs, we need to offer people an incentive to not only buy an EV, but to scrap their current petrol or diesel car. EVs shouldn’t be the reserve of the affluent. A phased scrappage scheme for all internal combustion engine vehicles that enables a sensible transition to EVs should be introduced.
The costs of batteries have fallen faster than even the most optimistic forecasts, which means the future for EVs is looking very bright. The UK Government had previously committed to banning the sale of new conventional petrol and diesel cars by 2040. The Committee on Climate Change has described this target as not ambitious enough, and recently recommended that all sales of new cars and vans need to be ultra-low-emission vehicles by, at the very latest, 2035. The UK Government needs to adopt this as a formal target, giving a clear indication to industry that the EV is going to be the only horse in the race by the middle of this century.
The building of public charging points needs to be ramped up considerably if we’re to meet the 2050 target and these need to be standardised, so any vehicle can use any charging point. It would be a gamble to rely on the market to provide a charging network without incentives from central government. The market for building charging points won’t exist without EVs, and take up of EVs isn’t going to happen at the speed we need if the charging points aren’t accessible for every day users.
The decisions on where to situate that charging network needs to be taken at a local level; different parts of our cities and towns are more suitable for building on-street charging points or public charging points than others. Solutions which involve portable charging points (a van filled with batteries) have been proposed, but a one-size-fits-all approach isn’t going to work. Local authorities are best positioned to make those decisions, so funding from central government needs to be made available at a regional level.
So, when it comes to helping to save our planet through electricity, there are some relatively straightforward, but important steps we can take today. Through advanced materials and new and innovative kinds of research, there are also many possibilities for protecting our future.
By being creative, thoughtful and bold with our current technologies, we have the immediate power to address a global challenge and, ultimately, safeguard humanity’s long-term survival.
Dr Richard Fields is a former Research Associate and Electrochemical Research Engineer at The University of Manchester's Graphene Engineering Innovation Centre.
Case study: fast-track innovation in running shoes, with a local SME
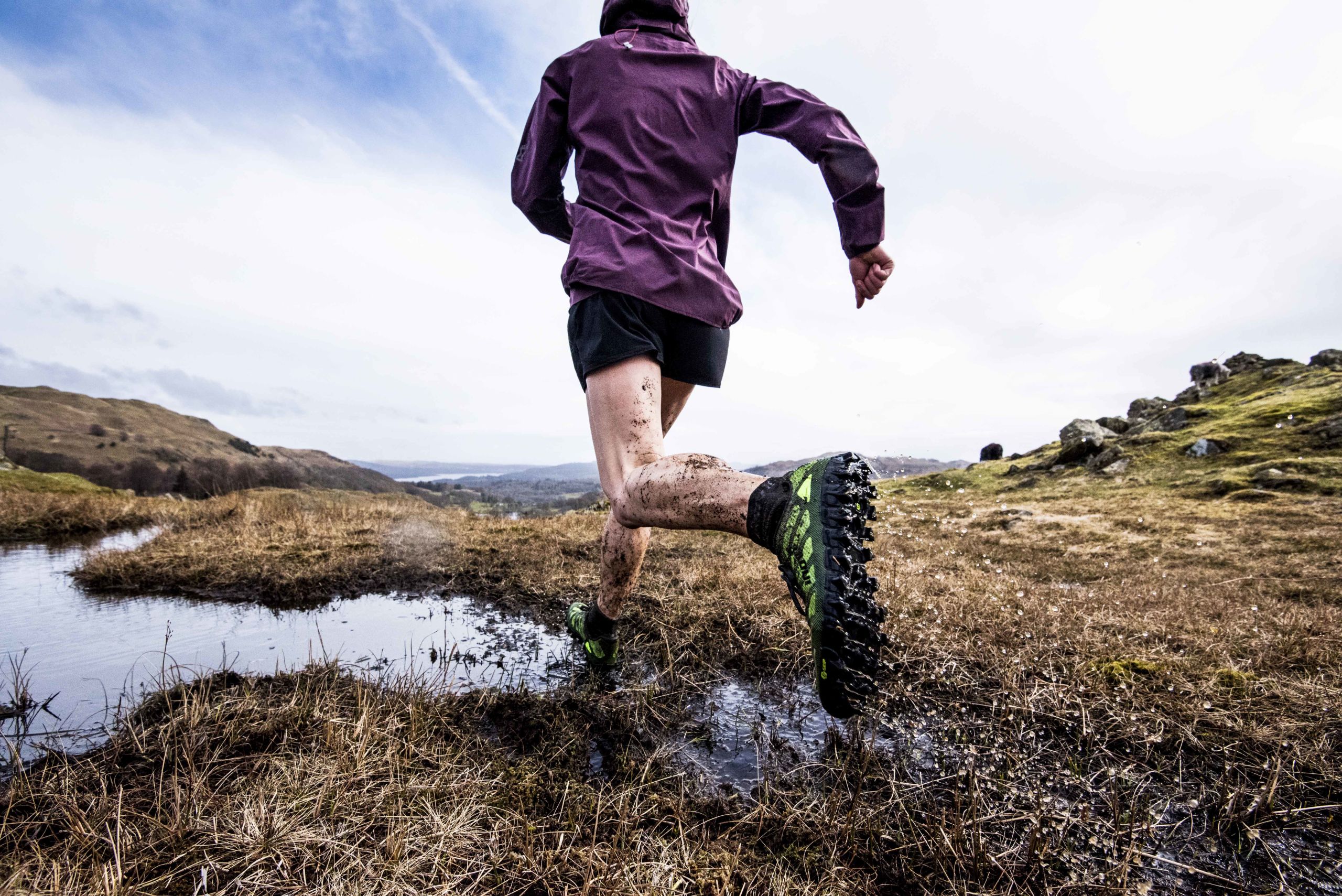
Graphene has moved from the first sample produced in a Manchester lab to commercial use in high street products in 15 years – extremely fast for a completely new material.
Different applications, different timescales
How we use various materials dictates what qualities those materials need to have. Similarly, how we use materials and products dictates the different levels of testing and validation required. For example – new electronic materials for ICT require exceptional quality at a low price; new composite materials for aerospace need to undergo decades of testing and validation; whereas for other applications like sports, where performance can be prioritised over price, new composite materials can be adopted much faster. For instance, many new technologies are first developed for motorsport before they then go on to reach everyday customers in their family saloons.
Innovators and risk-takers
SMEs are sometimes willing to take the risks of adopting new materials and technologies, in an effort to gain a competitive edge over their established and larger-scale players. In the case of graphene as well, SMEs have also been more ready to adopt this revolutionary material to produce market-disruptive products.
The agility of SMEs makes them able to introduce new materials and technologies faster, due to their smaller but more focused product portfolio and close-knit teams.
From lab to prototype to product
In 2016, we published research showing the improvements that graphene can bring to ‘stretchy’ materials, like natural rubber and polyurethane, and the story was picked up by local media. This press coverage was noticed by Inov-8 CEO Ian Bailey, who recognised the potential in adopting this novel material to bring a step change to his specialist running footwear brand.
This idea was then developed with support from an EPSRC Impact Acceleration Account (IAA) award, followed by an ongoing Innovate UK Knowledge Transfer Partnership (KTP) award, to create the graphene-infused outsole rubber.
The duration from start of the project in January 2017 to the first promising compound was less than a year, in which period we trialled and tested over 20 compounds in the lab. This was followed by prototype shoes that were field-tested by athletes in all kinds of terrains across the world.
The world’s first graphene-enhanced running and fitness shoes were introduced by Inov-8 into the worldwide market in June 2018, just 18 months after the project started. Only six months later, Inov-8 then launched the world’s first graphene-enhanced fast-hike shoes and boots.
The shoes have won numerous industry awards, and are being worn by athletes across the world, including Jasmin Paris, who earlier this year broke the 268 mile Spine Race world record by more than 12 hours.
A number of further developments in the use of graphene in sports footwear is expected in the coming months and years.
It has been an exciting journey for us and Inov-8 - a collaboration that continues to flourish.
Dr Aravind Vijayaraghavan is a Reader in Nanomaterials at The University of Manchester.
Dr Maria Iliut is a Materials Engineering Research Associate at The University of Manchester's School of Materials.
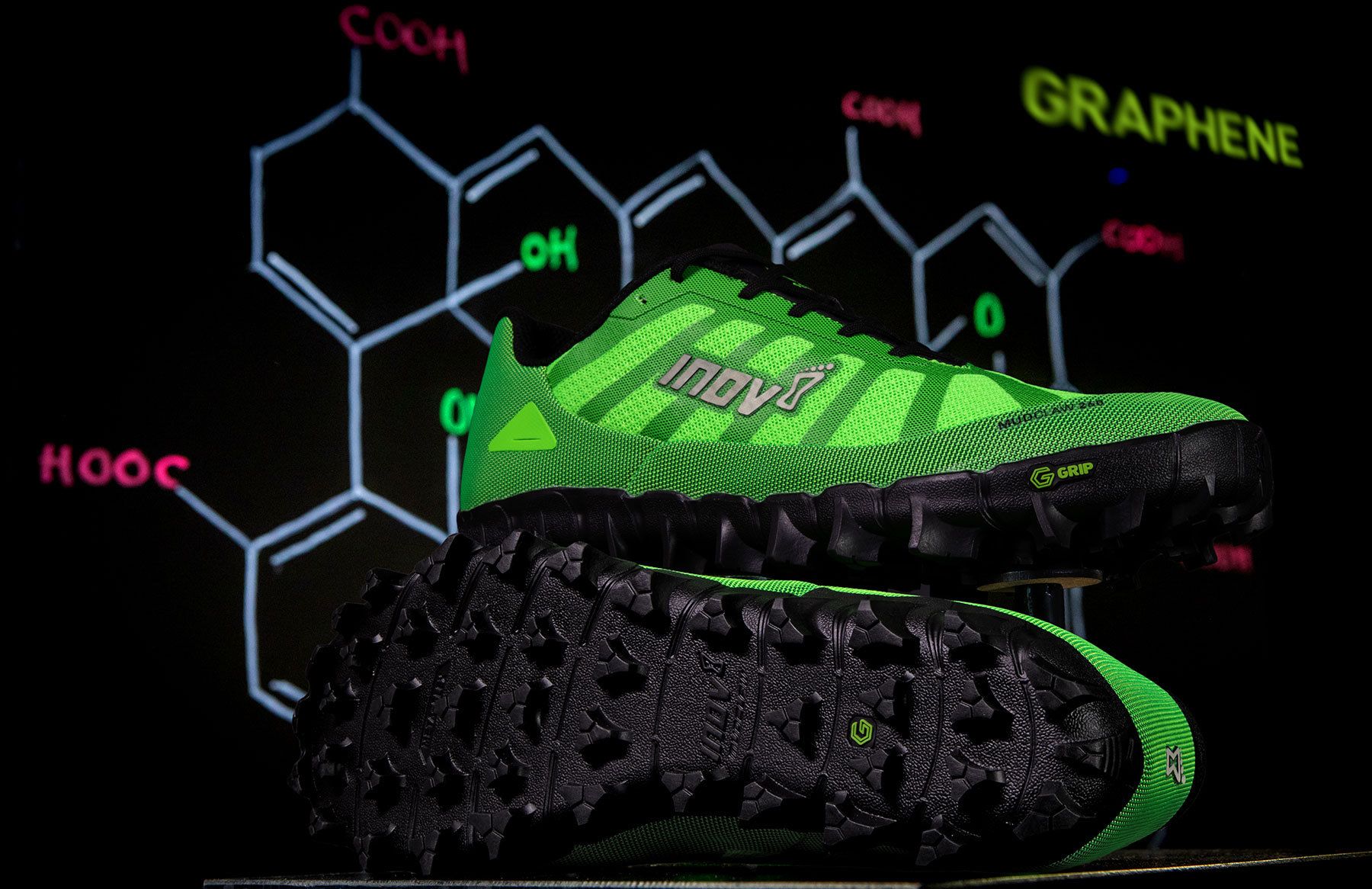
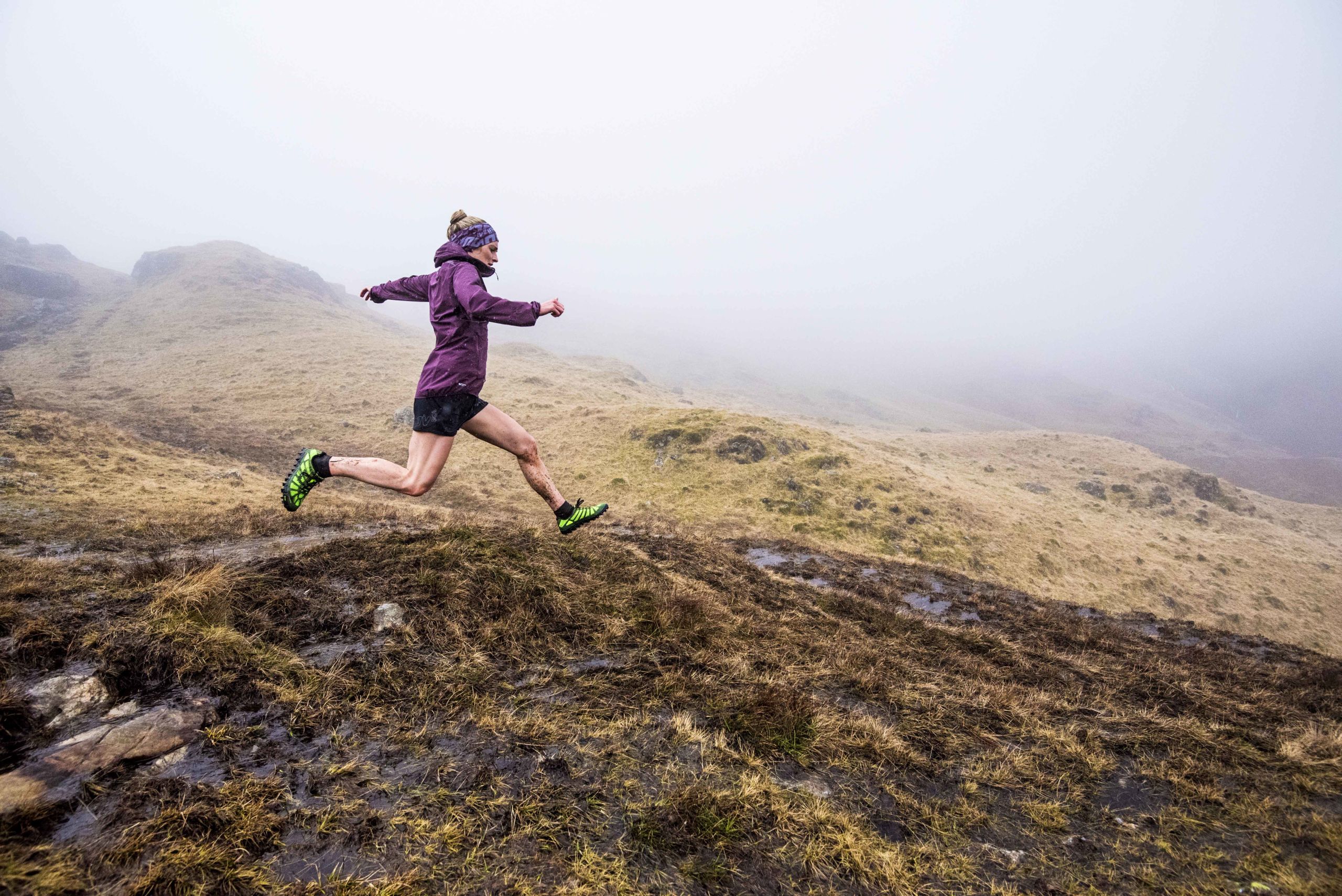
We're only scratching at the surface: why surface engineering matters, to our city, and beyond
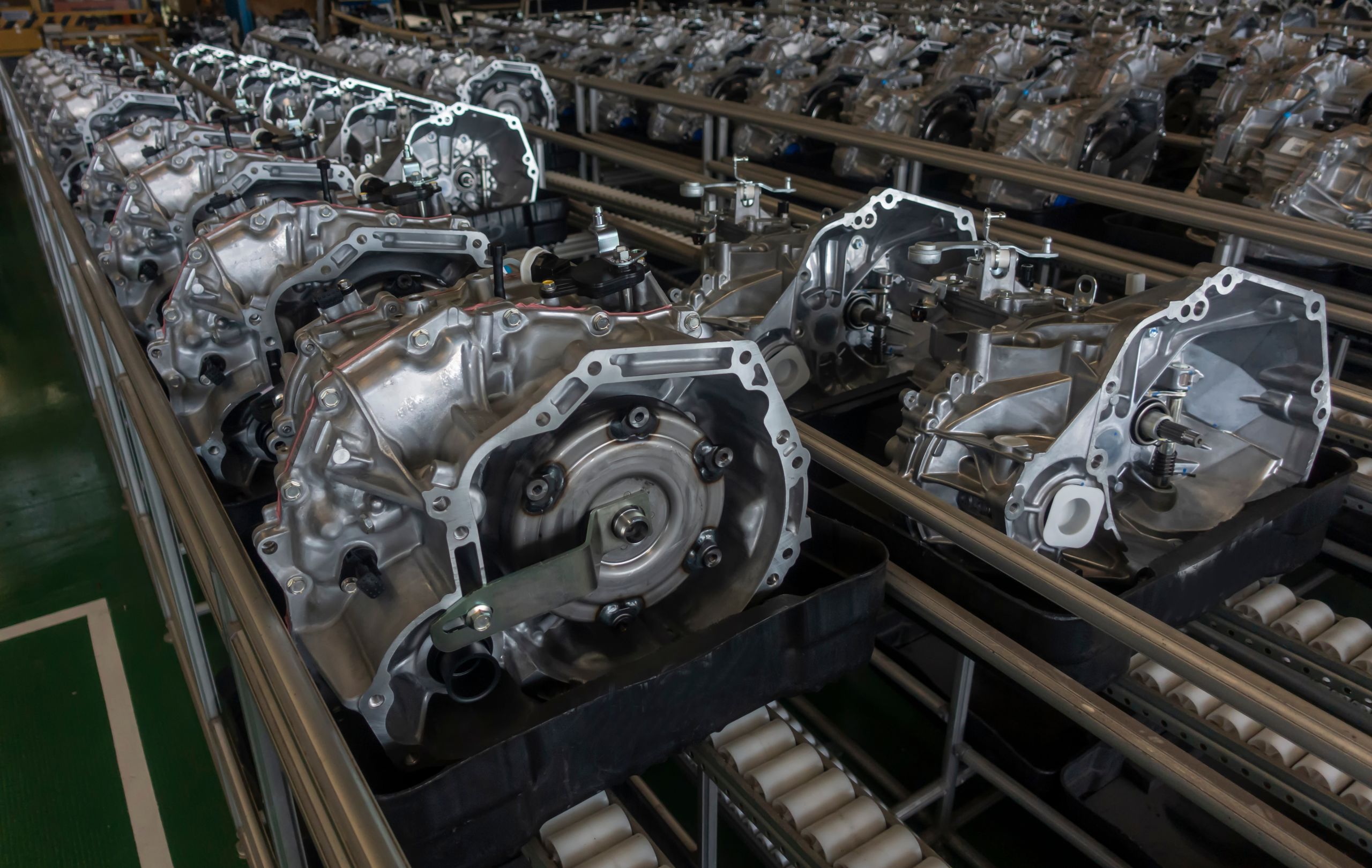
As important as developing new materials is, it is often the changes to the surface of an existing material that achieves the greatest benefits to performance. Surface engineering is about modifying the surface of what lies beneath, to make it perform better, last longer, or even achieve a different function entirely. Surface coatings are no small matter. Aeroplanes, for example, can’t take off without protective coatings in their engines.
A route to sustainability
So, surfaces can prevent or control the main ‘life’- determining characteristics of materials (such as wear, corrosion and fatigue). But they can also have a huge impact on sustainability, for example by ensuring optimised use of scarce materials in mobile phones and by reducing energy losses due to friction in car engines.
A billion-pound industry
Given the widespread use, versatility and practical importance of coatings, it isn’t surprising that the coatings industry in the UK is worth over £11 billion each year, and that coatings are used in products worth over £140 billion. Surface engineering is a dynamic, vital and extremely high-value industry but it’s perhaps not as widely appreciated or understood as it should be.
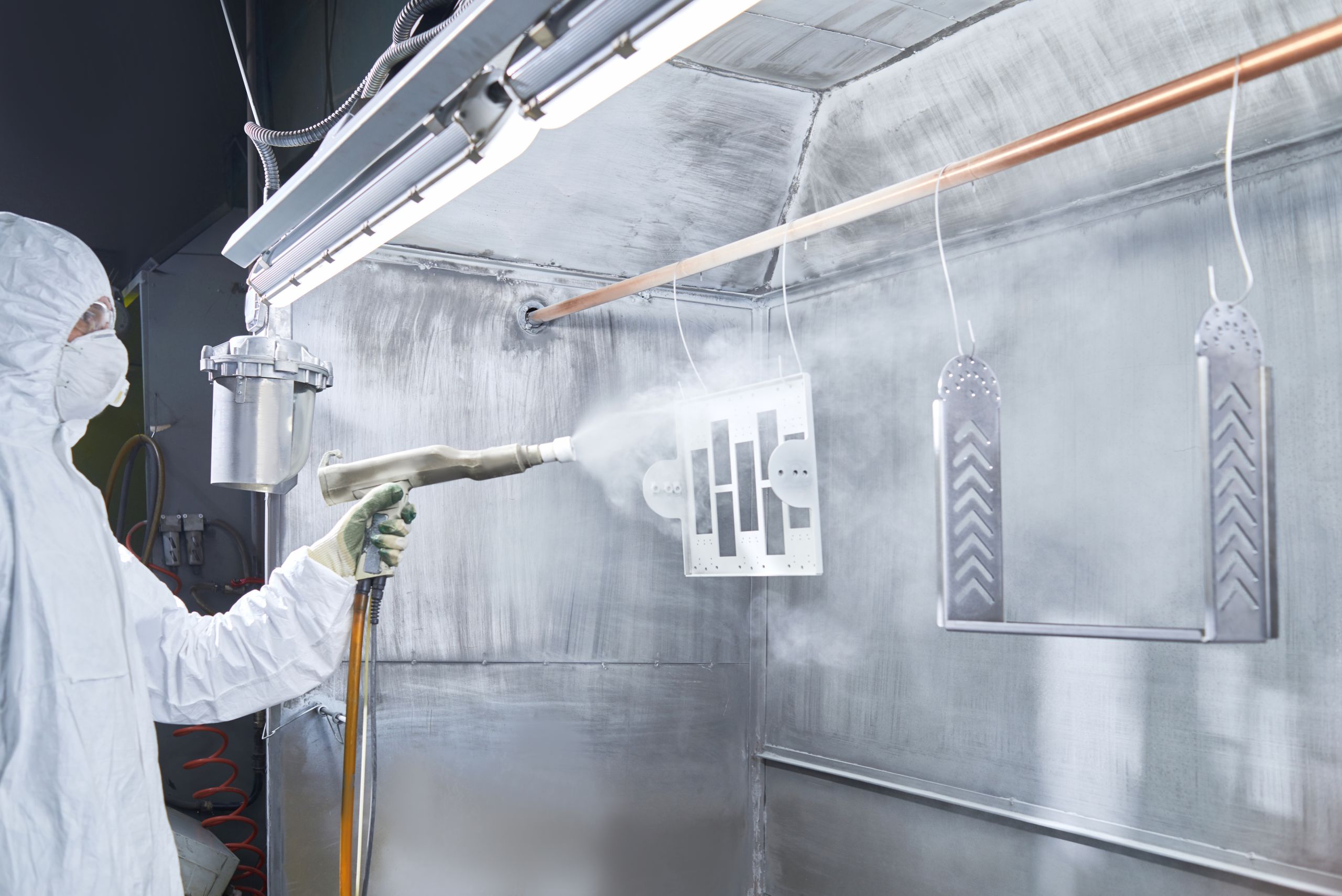
The term ‘surface engineering’ has been in use since the 1980s, but outside of those who work in this field, many people probably don’t appreciate how much of a difference it makes to their everyday lives. For example, we tap on computers that operate thanks to the functional thin films in their memory devices and touch screens.
The Fourth Industrial Revolution
The UK Government has, as part of its Industrial Strategy, made a joint commitment with industry to invest in the digitisation of manufacturing, paving the way for the UK to embrace the Fourth Industrial Revolution, or Industry 4.0. Surface engineering impacts all industrial sectors and stands to achieve an even greater impact by embracing digital technologies, not only in the coating processes but also in the coatings themselves as well as the products which incorporate the coatings.
Manchester’s pivotal role
The 2016 Greater Manchester and East Cheshire Science and Innovation Audit identified advance materials as a strength of the region – something that is attracting people, jobs and investment to the area.
We need to maintain that impetus. Surface Engineering must be considered as a vital part of that broader picture, within the forthcoming Local Industrial Strategy to ensure Greater Manchester confirms its position as a global leader in materials innovation.
Researchers like myself benefit greatly from the help of local policymakers. The Greater Manchester Independent Prosperity Review highlighted again that Manchester has a world-class strength in the form of advanced materials, and that this high productivity sector should be a focus for the Greater Manchester Local Industrial Strategy. Let’s make sure surface engineering continues to be a key part of that conversation.
Professor Allan Matthews is a Professor of Surface Engineering and Tribology at The University of Manchester's School of Materials, the Director of the BP International Centre for Advanced Materials and a Fellow at the Royal Academy of Engineering.
Learning from nature: a sustainable bio-based future?
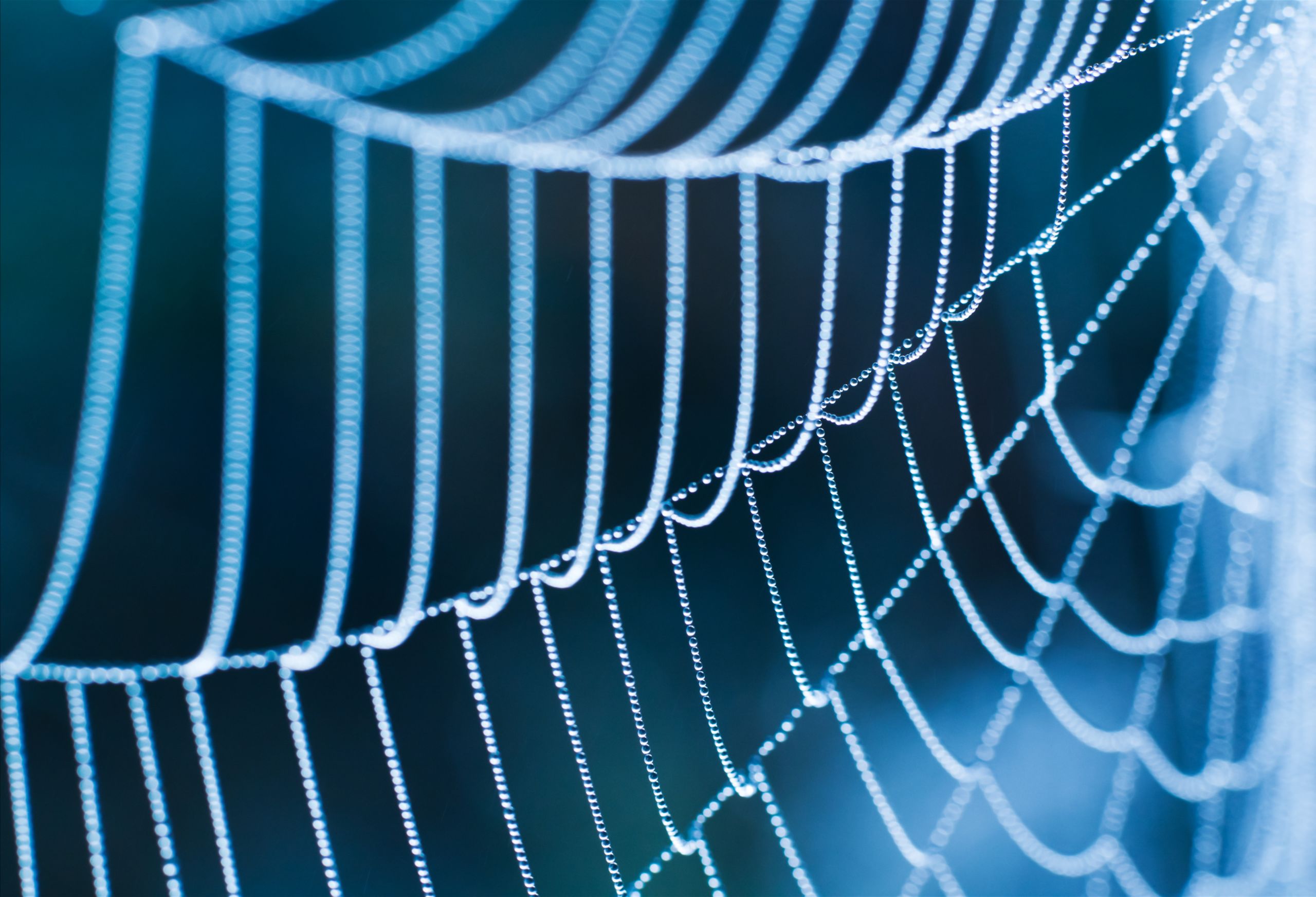
20th century advances in chemistry revolutionised material science, fundamentally changing global society. Plastics now underpin every aspect of modern life, from food to fashion, and from mobile phones to medicines. But in recent times we have come to realise that this petrochemical boom is leading to an environmental bust, with plastics now contaminating soil, water and food chains across the Earth. We need a fundamental rethink on the way we manufacture and dispose of materials.
Nature’s catalysts
One of the most innovative and promising routes to tackling these materials challenges is through biology. Industrial Biotechnology (IB) is the application of nature’s catalysts - enzymes - and biological systems, to produce and process materials, chemicals and energy. It is a burgeoning area of science, with recent developments in the field of synthetic biology giving us the ability to adapt biological systems for useful features to apply to a wide range of pharmaceuticals, chemicals and materials, for example meat that ‘tells us’ when it’s going off, reducing food waste and saving money.
Scientists at the University’s Manchester Institute of Biotechnology (MIB) are at the forefront of the UK’s efforts to apply IB to materials science and there are three main avenues for this research: biomanufacturing of sustainable plastics, ‘end-of-life’ degradation and recycling, and next generation bio-inspired materials.
Biomanufacturing of sustainable plastics
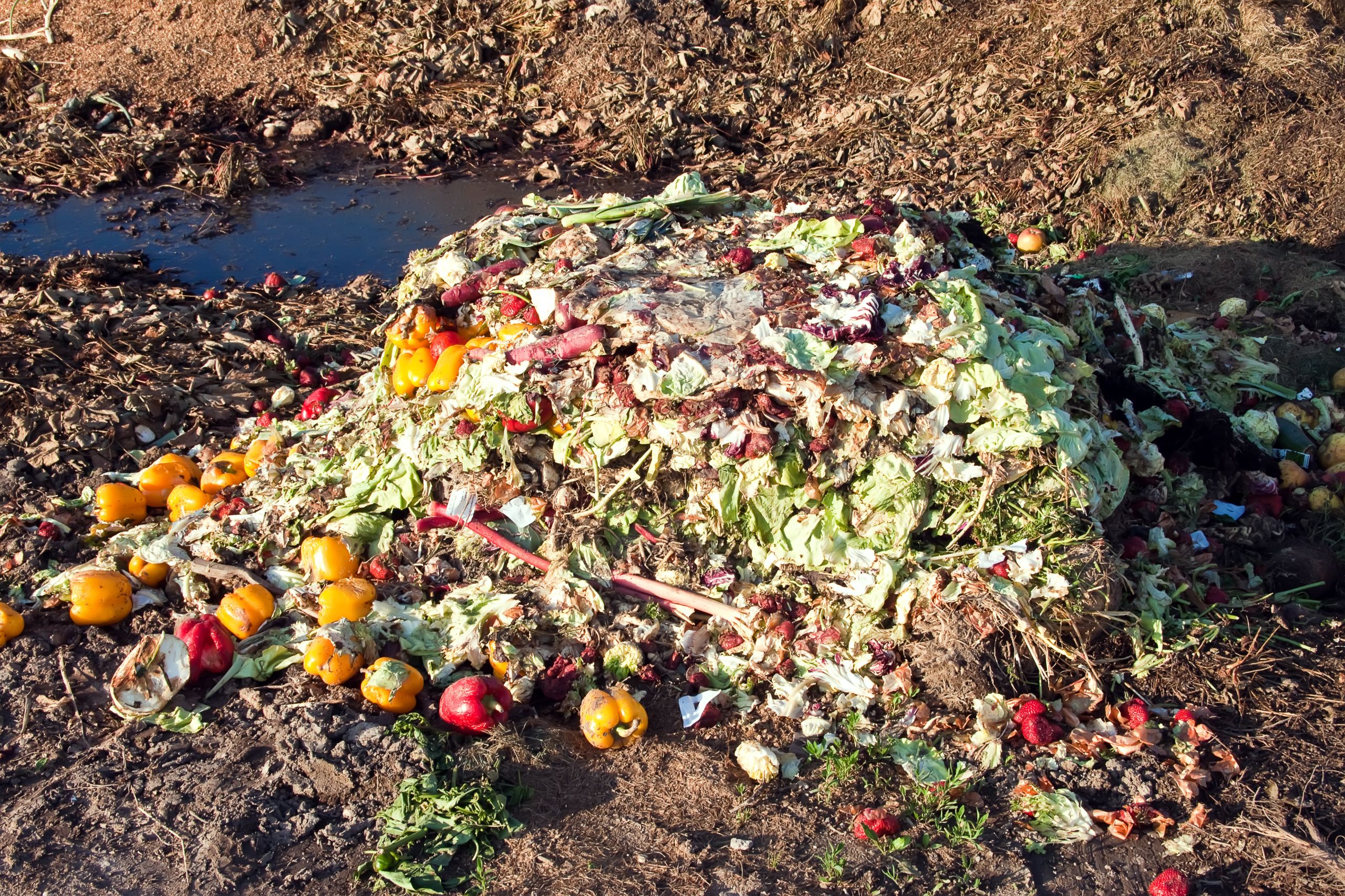
Instead of manufacturing plastics from crude oil, IB gives us the ability to produce bio-based materials from alternative carbon sources, such as non-food crops, or even agricultural waste. This is already happening at the industrial scale, for instance international chemical giant BASF switched its global production of acrylamide (the precursor to polyacrylamide, a widely used plastic) to an enzyme-based process, and all the major tyre producers are investigating IB-produced alternatives to natural rubber. But, whilst ‘drop-in replacements’ to traditional ingredients might lower the carbon footprint of the final product, this isn’t an environmental panacea; for example, a polymer derived from bio-based feedstock isn’t necessarily biodegradable. Polyethylene produced via biotechnology has the same chemical properties as oil-derived, non-biodegradable polyethylene. So, a bio-polyethylene bag bought from your local supermarket isn’t necessarily going to be biodegradable simply because the polyethylene used was produced in a different way.
Low cost, sustainable production of common plastics is challenging, but this is a priority area for the Future Biomanufacturing Research Hub (Future BRH). A new UK national centre, the Future BRH is developing innovative biotechnologies for high-value manufacturing to sustainably produce pharmaceuticals, chemicals and materials. Scientists here are developing robust industrial microorganisms that can be grown in non-sterile environments, such as in seawater, both reducing costs of getting from lab to product, and reducing freshwater demands.
‘End-of-life’ degradation and recycling
The microbes that live alongside us are starting to adapt to the waste that we’re putting into the environment. Some have naturally evolved to produce enzymes that can use plastic to create energy. MIB researchers, in partnership with the Henry Royce Institute for Advanced Materials, are seeking to ‘supercharge’ these natural evolution processes to engineer enzymes orders of magnitude faster by using a directed evolution approach. What would this mean in practice? It could mean much better recycling and far less environmental damage. The material used to make many ‘degradable’ coffee cup lids looks the same to the sorting machinery at the recycling depot as the plastic used to make clear soda bottles. But they can’t be recycled in the same way, and any contamination – if you put your coffee cup lid in the wrong bin – could mean that the whole batch is spoiled. Using enzymes to degrade these contaminants so they don’t have to be sorted by hand could lower the cost of recycling as well as creating better recycled products.
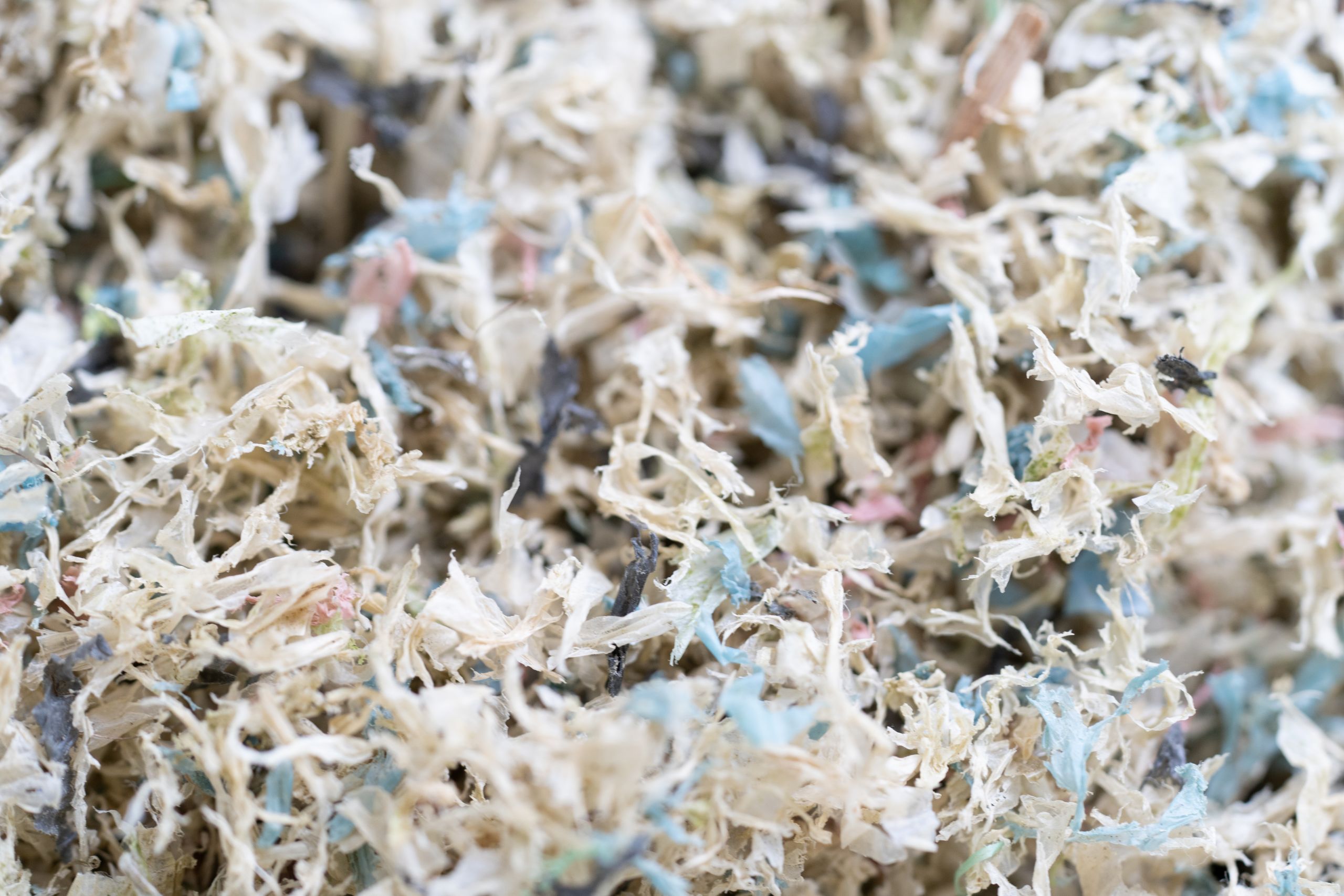
Next generation bio-inspired materials
From the sticky, stretchy or stiff kinds of silk found in spiders’ webs to the resilient properties of nacre (mother of pearl), the natural world has evolved an enormous variety of materials with desirable mechanical properties, such as enhanced strength, flexibility, adhesion and transparency.
Scientists are now taking a fresh look at nature to feed the development of new bio-inspired advanced materials. By drawing on knowledge gained in more established IB fields, such as pharmaceuticals, we have a toolbox of new enzymes to access novel chemistry that is difficult to reach with traditional methods. When combined with the latest computer-aided design software and laboratory automation, this IB approach gives a powerful platform to create exciting new biomaterials for a wide range of applications. Already, MIB research has led to optical coatings that can manipulate light, lightweight spider-silk derived composites with enhanced strengths, and new healable materials that can form protective coatings.
Cross-working and managing risk
The biomanufacturing of materials requires cross-disciplinary research, bringing together chemistry, mathematics, microbiology, synthetic biology, process engineering and materials science. But the transition to a sustainable bio-based future cannot occur in an academic vacuum, it also requires collaboration with industry, across multiple sectors.
The step-out nature of this R&D will require co-investment from Governments and international bodies to reduce the risk of investment for companies, especially SMEs. The UK Government’s Bioeconomy Strategy (published December 2018), outlined a vision to double the size of the bioeconomy by 2030. Government recognition of the importance of IB in delivering this vision is welcome but there must also be financial support for companies who want to develop biomanufacturing knowledge and capabilities.
Looking to the future: barriers and opportunities
In 2014-15, a dedicated research council fund was established, the IB Catalyst, which proved to be a highly effective way of sharing of risk in commercialising biotechnology; sadly, funding is currently on-hold. It is vital that this or an alternative dedicated funding source be reinstated to support academic and industrial partnerships to develop IB into sustainable real-world applications.
The UK is well positioned to become an international industrial biotech innovation and commercialisation hub, and a major contributor to clean economic growth. Manchester has the potential to be right at the heart of this – especially with the opening of the Future Biomanufacturing Research Hub. Industrial biotechnology was singled out in the Greater Manchester Independent Prosperity Review as being a ‘fast growth opportunity’, where Greater Manchester’s ‘assets and capabilities’ offer scope for future development.
To fully realise this potential, Industrial Biotechnology needs the establishment of its own Sector Deal – just as the Nuclear, Offshore Wind and Artificial Intelligence sectors have received from the Department of Business, Energy and Industrial Strategy. These deals demonstrate a clear direction and priority from the UK Government and would give investors and industry the certainty they need.
With the right investment, biomanufacturing could support the UK’s Clean Growth aim to take pollution out of economic development and allow us to transition to a new sustainable ‘Materials from Biology’ era.
Dr Kirk J. Malone is the Director of Commercialisation at The University of Manchester's Manchester Institute of Biotechnology.
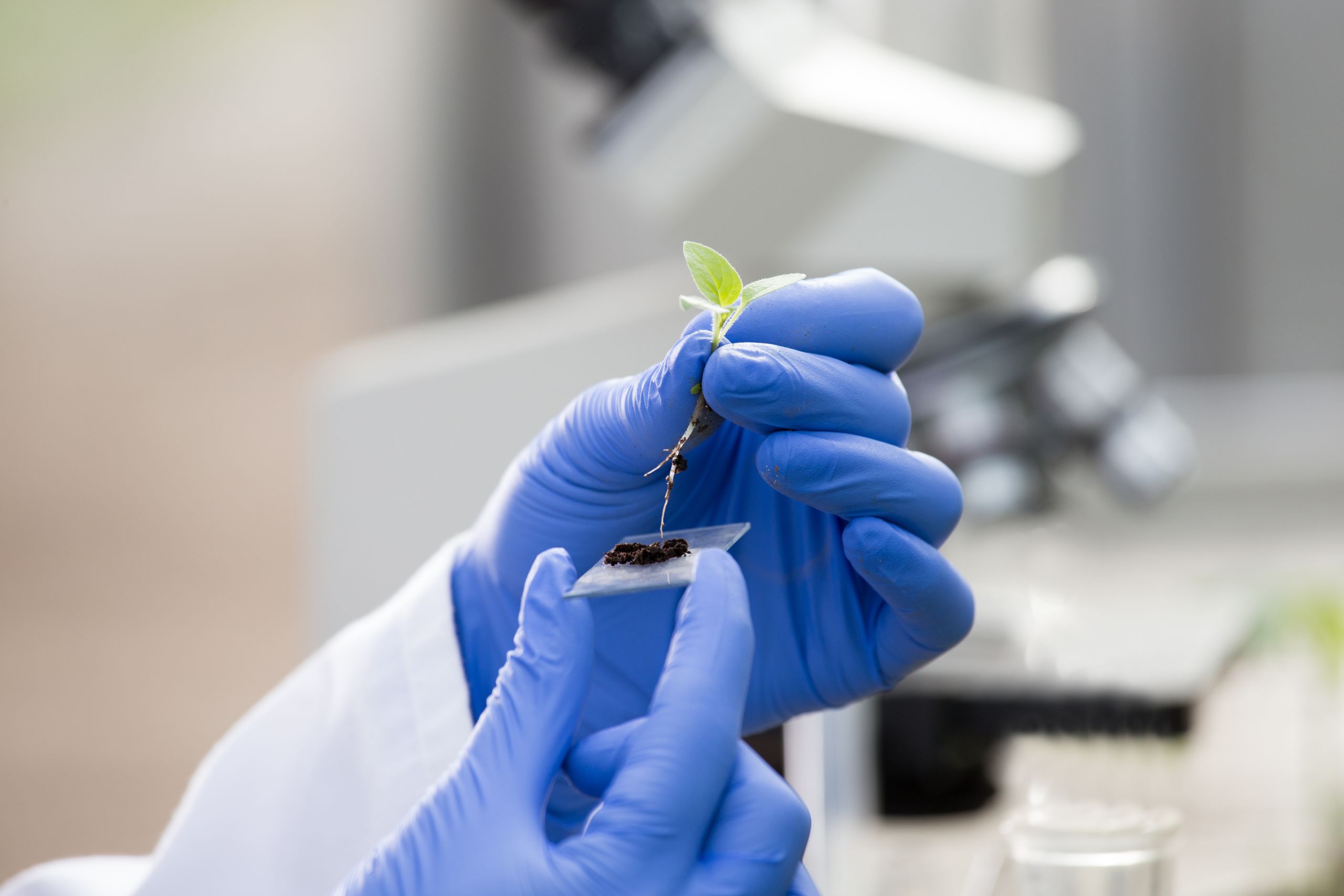
Innovation on the front line: rebuilding bodies with ‘Bone Bricks’
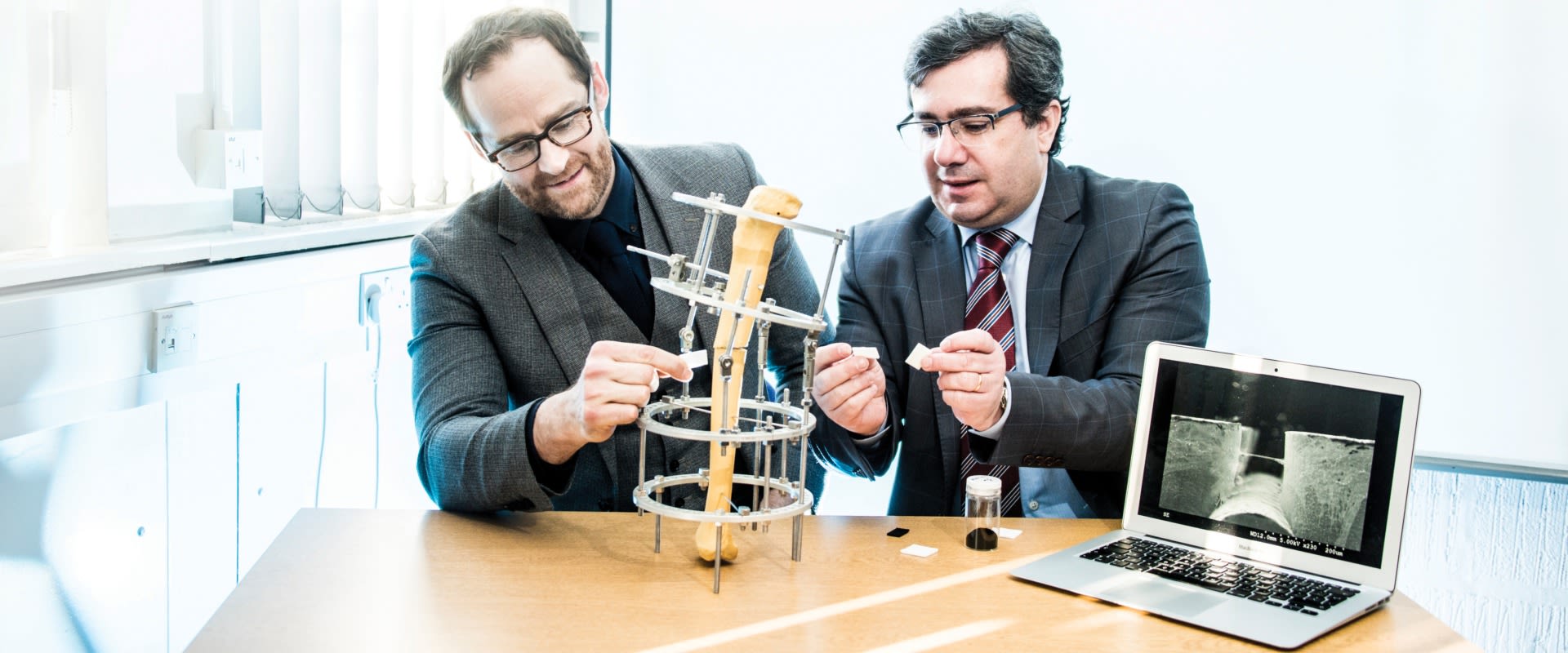
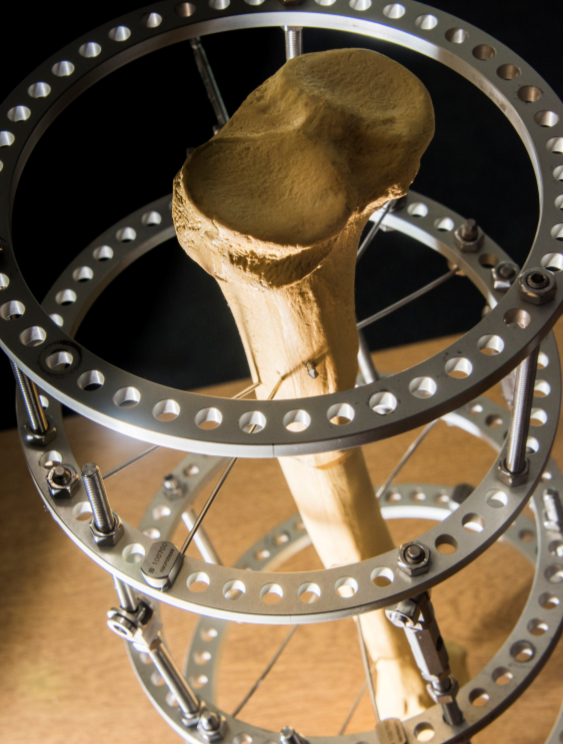
Bomb blast injuries can cause devastating damage to bones, damage that is extremely difficult to fix. In response, we led a team that combines biomaterials excellence with limb injury expertise to develop a revolutionary ‘Lego-like’ brick system for bone repair. We believe this pioneering project, which takes a radical concept from the lab - and places it into the hands of clinicians on the front line – provides a strong model for the UK’s strategy to meet global challenges through research and innovation. It demonstrates how advanced materials can play a key part in providing solutions to the challenges we face. As well as showing how integral universities are in finding those solutions by pushing forward innovation with unique collaborations across the world.
A problem that needed a solution
When you see the damage of what a blast injury can do to a person - to a child – it’s a shock and very sad and upsetting to see. We first became fully aware of this type of injury when Amer Shoaib, a consultant orthopaedic surgeon at Manchester Royal Infirmary, came to the University to discuss his experience of treating barrel bomb blast injuries in Syrian refugees. Mr Shoaib is a limb injury expert with experience of working on the frontline of various conflicts as a humanitarian worker. When he described how the after-effects of blast injuries were sometimes untreatable in Turkey’s refugee camps, we all wanted to help and apply our expertise to the problem. We continued our discussion late into the evening and this developed into the idea of ‘Bone Bricks’, and led us on a journey to Turkey where we met with academics, surgeons and medical companies.
Bone injury & a new biomaterials ‘brick’ approach
The Bone Bricks pilot project was born, seeking a solution to the kinds of bone injuries caused by explosions which can result in contaminated wounds, shattered bones and substantial bone loss.
We have treated similar injuries in the UK, for example following terrorist attacks. In our hospitals, such patients can access expert orthopaedic surgery and equally important aftercare. However, in a remote border clinic with limited resources, this is just not possible. Amputation - an irreversible act which has a sudden and emotionally devastating impact on the patient - is unfortunately a frequent outcome in many of these cases.
With many blast injuries, the bone defects are impossible to heal on their own. What our project is doing is to create a temporary structure using ‘bricks’ made of polymer and ceramic materials, which can be clicked together like Lego to make a kind of medical scaffold which then allows new tissue to grow. Our pioneering structure will support weight like a normal bone and induce new bone growth as the degradable Bone Bricks dissolve. These interchangeable Bone Bricks also feature a specialist filler that has infection-fighting properties, vastly improving the chances of success.
The idea is that the surgeon can open a bag of bricks and piece them together to fit a particular defect. We will also be developing software to allow the clinician to select the exact number, shape and size of Bone Bricks, based on the individual defect, along with information how to assemble them.
A year into the project the impact of blast injuries was brought cruelly to our own doorstep following the devastating Manchester Arena attack in 2017. This incident involved a shrapnel-laden homemade bomb being detonated just as people were leaving the packed Arena complex following a concert by the American pop singer Ariana Grande. A total of 23 people died, including the attacker, and 139 were wounded - more than half of these were children.
We didn’t expect this so close to home - but the kind of technology we are currently developing would have been very helpful for many of those victims.
Innovation and the role of universities
Our project is an example of innovation on the frontline and we believe this is something only universities can do. Populations in crisis or living in the poorer parts of a developing region may encounter a number of agencies offering support. For example, the British Council, part of the Foreign and Commonwealth Office, can help with education and skills training while NGOs may provide aid or build operational infrastructure. But what universities can do is focus on a major issue affecting a hotspot and look to develop a bespoke solution that is based on rigorous research, and future-proofed.
Global challenges, British research
The Bone Bricks project is now an established partnership between The University of Manchester, University of Portsmouth, Manchester Royal Infirmary and Turkey’s Sabanci University. It has received approximately £0.85 million in funding, following backing from the Global Challenges Research Fund (GCRF), a £1.5 billion pot provided by the UK government to support cutting-edge research that specifically addresses the challenges faced by developing countries.
This globalisation of British research has been underpinned by the International Research and Innovation Strategy which sets out how the UK will develop international research and innovation partnerships to address global challenges while working towards the targets of the domestic Industrial Strategy. One of the strategy’s primary objectives is to connect researchers and entrepreneurs in a bid to “support their development and the translation of their ideas.”
The GCRF fund wants to support disciplinary and interdisciplinary research, including an expectation that researchers will consider an application of their research in an area they never previously considered. That was definitely the case for our Bone Bricks project; until we encountered Amer and his frontline work with those suffering catastrophic bone injuries, this was not a challenge we had considered for our work in biomaterials. It took time to fully appreciate the complexity in terms of the clinical challenges in the field, the wider geo-political impact, the potential commercial and intellectual property opportunities, as well the potential legacy applications for both developing and developed nations.
This type of complexity has led to concerns that ‘global challenge’ innovation is at risk from a range of factors. These include a lack of buy-in from target communities; poor coordination between delivery partners which could lead to duplication of efforts; poor portfolio management resulting in a package of discrete projects rather than a coherent set of responses to specific challenges; being able to demonstrate value-for-money; and, perhaps worst of all, a failure to create real impact in developing countries.
However, our project can avoid these risks because we will be applying the lessons learnt from the Manchester Model of lab-to-market innovation, developed by The University of Manchester’s advanced materials community.
Our project will be:
- Engaging with frontline clinicians and potential end-users to design a best solution rather than making do with existing products or procedures that are not fit-for-purpose
- Applying Manchester’s world-wide leadership in materials science and bioengineering to a global challenge
- Using Industry 4.0 technologies to accelerate concept development, for example using computer modelling and digitally-based manufacture techniques, such as 3D printing
- Ready to trial on patients soon after completing the three-project life-cycle
- Complying with health care regulatory regimes while the academic team is working with commercial partners to scale-up and bring the product to market
Looking to the future
In terms of next steps, to get this innovation manufactured and distributed worldwide, a separate, follow-on project will be funded by the Scientific and Technological Research Council of Turkey. Working with Sabanci University in Turkey and orthopedic innovators Response Ortho, a clinical trial will run on about 20 patients with large bone loss who have no other possible treatment other than amputation, subject to strict ethical scrutiny and approval.
Intellectual property (IP) will be jointly managed between all of the project partners and any revenue generated from this will be used either to further develop the product or to develop similar medical devices for other countries.
The Syrian conflict has displaced around three million refugees into Turkey, which provides free-of-charge healthcare services to Syrians. The burden on the healthcare system is significant, with 940,000 patients treated, 780,000 operations carried out and 20.2 million outpatient services used. The hope is that this UK innovation can in some way make a contribution to this crisis. More broadly, with innovation and research like this, universities are uniquely positioned at the centre of a global network. They can support the channeling of overseas aid towards frontline innovation in areas of conflict. The benefits from products made from advanced materials should not just be for developed nations, where funding is often more readily available and supply chains are already more established.
The long-term vision for the project is that Bone Bricks will help in conflict situations and healthcare emergencies more widely, for example, in road traffic accidents in both developing and developed nations. The Bone Brick solution is much more cost effective than the current methods of treatment available, at less than £200 for a typical 100mm defect, compared to upwards of £6,000 per limb reconstruction procedure. Also saving limbs as opposed to amputation will equate to an estimated reduction of two thirds of the treatment costs. The project could also reduce the need for expensive surgical reconstruction for bone loss, as well as reducing the losses to the economy of extended periods of rehabilitation.
Bone Bricks is a sustainable, cost-effective, cross-sector initiative that takes cutting-edge research from the lab to where it’s needed most. It is an example of pioneering innovation in the fast-changing field of advanced materials. But more than that, it is an example of how overseas aid can drive innovation both for those in conflict zones and back in the UK.
Professor Paulo Bartolo is the Chair of Advanced Manufacturing at The University of Manchester's School of Mechanical, Aerospace and Civil Engineering (MACE).
Dr Andy Weightman is a Lecturer in Medical Mechatronics at The University of Manchester's School of Mechanical, Aerospace and Civil Engineering.
Dr Glen Cooper is a Lecturer in Solid Mechanics and Bioengineer at The University of Manchester's School of Mechanical, Aerospace and Civil Engineering.
We need an ‘Internet of Materials’ to get from lab to market faster
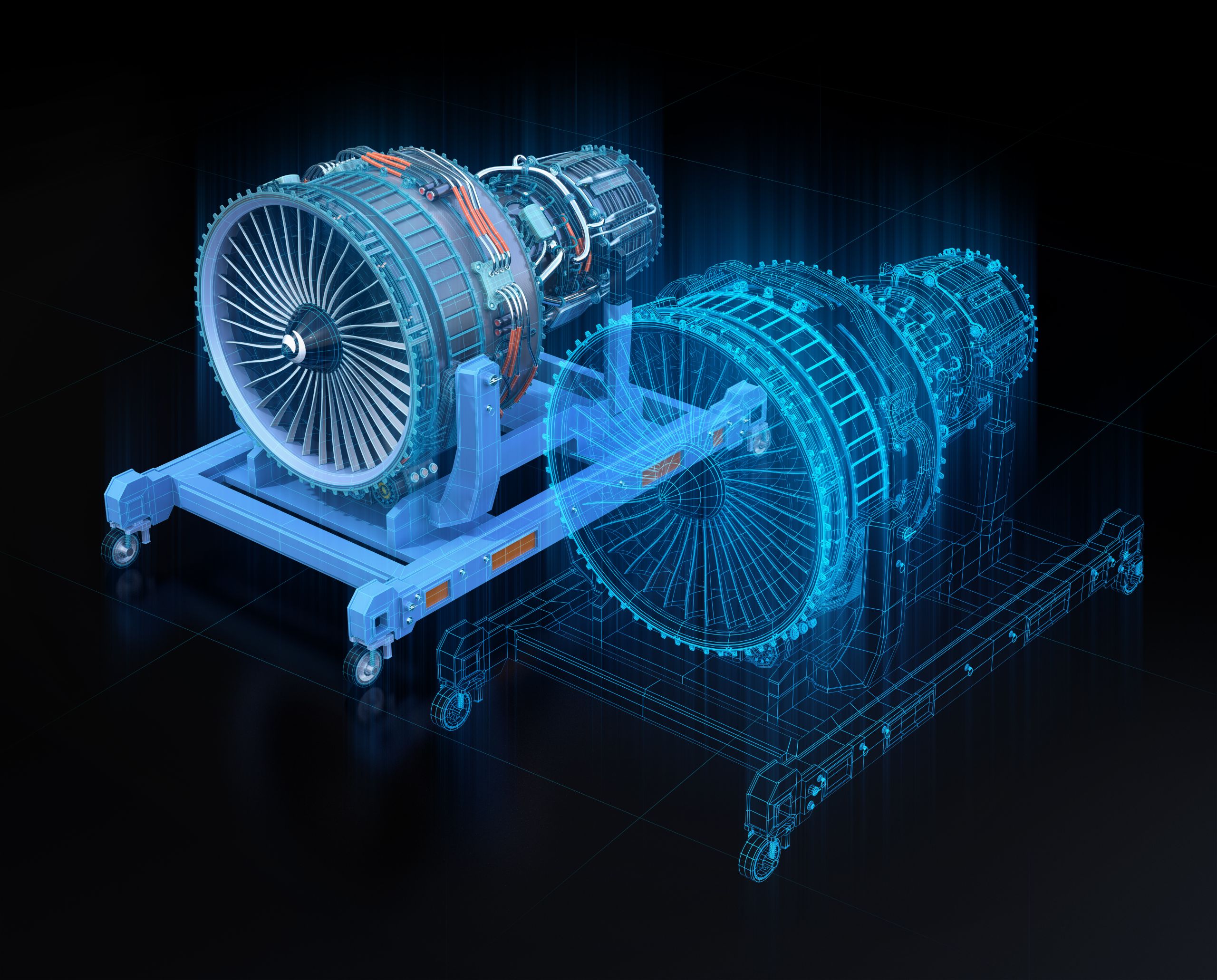
New materials, or materials systems, expand the horizons of what we can achieve, but developing one is expensive and the time from lab to market is long. That development can be completely derailed by an unexpected problem, or a competitor can get to market first – meaning all the time and the money spent is completely wasted. Even if that time and money produces a superior product, it’s usually the first to arrive that takes the lion’s share of the market. For an SME the risks are high because being beaten to market might bring down the company.
Risks, costs, and rewards
It can take decades to go from initial experiments in a laboratory to seeing new materials in products on shop shelves. For example, bioglass - the first artificial material found to chemically bond with bone - was invented in the 1960s and only found widespread medical application in the 1980s. It is now widely used for implants and to treat bone injuries, among other uses. Furthermore accelerating a material to the market too early can have serious consequences. For example, engineering carbon fibres were developed in the 1950s, and by the early 1970s this innovation was considered for the fan blades in the revolutionary Rolls- Royce RB211 jet engine. Unfortunately poor impact damage resistance to large objects (eg flocking birds) and spiralling costs, nearly brought down the company. Fortunately, because of its strategic importance, it was saved by the government of Edward Health and nationalised. Now, more than 60 years after carbon fibres were first developed, Rolls-Royce are again considering composite fan blades.
While the costs and risks can be very high, so are the potential rewards. A new material or process can utterly transform a sector, or even our lifestyle. Chances are you’re wearing something containing one type of plastic, about to eat your lunch using something made of another, or reading this on a device, predominantly made of plastics. And maybe this afternoon you’ve got a to-do list on a Post-it Note? Discovered in the late ’60s by Spencer Silver at 3M. Silver was initially tasked with creating a super strong adhesive. He failed, but out of failure temporary ‘sticky notes’ were born and now infest offices and team away-days around the world.
Harnessing big data
What are the options for speeding up this timeline, to reduce costs and allow smaller companies to innovate? We need to accelerate the design, make, test, characterise and iterate cycle (in other words the whole product development process), and couple this to advances in machine learning. We need to fail fast in the lab and learn quickly.
First, we need to be able to make and process many variations (designs) of a material quickly and cheaply in small quantities, then we need to quickly characterise all the variants to identify the most promising ones on which to focus the next iterations. In this respect, our ability to characterise materials has expanded greatly over recent years – a plethora of techniques are available to help us uncover the structure and chemical composition of a material - so there is inevitably a huge amount of data collected. But there’s a problem: most of the time that data isn’t as accessible as it could be, either because it is commercial property or because it isn’t digitally accessible.
The advantages of an ‘Internet of Materials’
Imagine a world where all the information obtained from analysing different materials is kept, stored and available. If you were a company looking to develop a new material, a quick search of this massive repository could potentially save you years of expensive R&D. This ‘Internet of Materials’ concept has been suggested to take advantage of our data-rich world and allow companies to prosper in the upcoming ‘data-driven’ era of industry. At the same time we need to refine manufacturing processes to control and optimise material functionality. This requires a much better knowledge of the manufacturing process and its effects through the automation, information from sensors and data exchange (the so-called Fourth Industrial Revolution of digitisation (Industry 4.0).
With such an enormous amount of data, it is possible to create a ‘digital twin’ of a component or system and its properties. This is already happening to some extent in the aerospace industry where developers are using data to create digital twins of the turbine blades in real engines to follow how and where they are being flown across the world. In this way, the engine manufacturer can, for example, predict the health of their blades as a function of their flight history. By following the state of the virtual digital twin the manufacturer can remotely ensure the real blades are flown within safe limits, inspected when necessary and safely withdrawn from service as it approaches the end of their operational ‘life’.
What next?
Where could all this lead to in the future? Our horizons have always been limited by the materials we have to hand, from the Stone Age to the approaching carbon age. However, I’d argue that materials science has never been so important; 21st century global challenges such as food and water security, global warming, dwindling supplies of critical elements and our burgeoning energy needs - all require new materials and require them quickly.
If we can accelerate the materials development cycle we could look forward to: biomaterials that help our bodies repair themselves before harmlessly dissolving away; tough ceramics able to withstand the harshest environments; ‘super-batteries’ that last much, much longer; membranes for water purification; devices able to harness energy from waste heat to run themselves; graphene-based neural interfaces to repair the nervous system; metals that actively inhibit rusting or smart clothing that responds to the environment or senses well-being. There’s no limit to what might be possible if we put our minds to it aided by the explosion in big data and machine learning.
Whatever happens, materials design needs to prioritise the sustainable use of materials, minimising waste and finding solutions to materials in critically short supply. We must develop plastics that can be reused, recycled, or biodegraded.
The establishment of the Henry Royce Institute for Advanced Materials is a response to these challenges. It has its £200 million hub at The University of Manchester it spans nine leading institutions – the universities of Cambridge, Imperial College London, Sheffield, Liverpool, Leeds, Oxford, the National Nuclear Laboratory and the Culham Centre for Fusion Energy. Working with UK academia and industry it aims to accelerate the invention and take up of new materials systems that will meet global challenges, to enhance industrial productivity and competitiveness, and help positively shape the world around us.
First steps
There is much to do if the UK is to maintain its world leading position in the development of new materials. We must look at ways to innovate faster and smarter with a more competitive edge and an eye on sustainability including:
- Develop small scale make-test-characterise capabilities to speed up development across the full spectrum of materials, from large components to nanoscale
- Give SMEs access to the same level of research, facilities and expertise that would be available to a major multinational company
- Agree more standard industry-academia contract arrangements to accelerate engagement of industry with single or multiple universities
- Get greater involvement of mathematicians to support the evolution of data within materials manufacturing
- Design methods and calculators that can provide sustainability information from the outset
Last, but not least, we need to exploit big data approaches and this means we urgently need to develop frameworks for the storing and sharing of all kinds of materials data.
An ‘Internet of Materials’ could, literally, change the world.
Professor Phil Withers is a Regius Professor of Materials at the School of Materials at The University of Manchester. In 2008, he set up the Henry Moseley X-ray Imaging Facility (HMXIF).
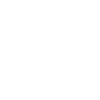
Contributors
Professor Luke Georghiou - Deputy President and Deputy Vice-Chancellor at The University of Manchester and Professor of Science and Technology Policy and Management in the Manchester Institute of Innovation Research
James Baker - CEO of Graphene@Manchester
Professor Sarah Cartmell - Professor of Bioengineering at The University of Manchester
Professor Mike Shaver - Professor of Polymer Science at The University of Manchester in the School of Materials
Dr Richard Fields - Former Electrochemical Research Engineer at The University of Manchester's Graphene Engineering Innovation Centre
Dr Aravind Vijayaraghavan - Reader in Nanomaterials
Dr Maria Iliut - Materials Engineering Research Associate at The University of Manchester's School of Materials
Professor Allan Matthews - Professor of Surface Engineering and Tribology at The University of Manchester's School of Materials, Director of the BP International Centre for Advanced Materials and a Fellow at the Royal Academy of Engineering
Dr Kirk J. Malone - Director of Commercialisation at the Manchester Institute of Biotechnology
Professor Paulo Bartolo - Chair in Advanced Manufacturing at The Manchester University's School of Mechanical, Aerospace and Civil Engineering (MACE)
Dr Andy Weightman - Lecturer in Medical Mechatronics at The Manchester University's School of Mechanical, Aerospace and Civil Engineering (MACE)
Dr Glen Cooper - Lecturer in Solid Mechanics and Bioengineer at The Manchester University's School of Mechanical, Aerospace and Civil Engineering (MACE)
Professor Phil Withers - Regius Professor of Materials at the School of Materials at The University of Manchester
Policy@Manchester, The University of Manchester
Additional editing by Katie Brewin Consulting
Created by Christina Cooper
The opinions expressed in this publication are those of various authors and do not represent the views of The University of Manchester.
June 2019
#OnMaterials
BoneBrick header image and Inov-8 shoe photograph ©Jill Jennings
